用于可燃气体信号采集的数字显示探头设计方案
1 系统工作原理
可燃气体报警器由传感器检测电桥、直流放大器、A/D转换单元、零点、量程调整单元、单片机以及报警显示电路和输出电路等部分组成。系统框图如图1所示。首先,传感器送来的与可燃性气体浓度相对应的微小电压信号经过放大后,由A/D转换电路将其转换成数字信号后送入单片机。单片机再对该数字信号进行滤波处理,并对处理后的数据加以分析,以确认是否大于或等于某个报警值。若大于报警值则启动报警电路发出声光报警,反之则为正常状态。然后该数字信号被送到显示单元以显示相应的浓度值。
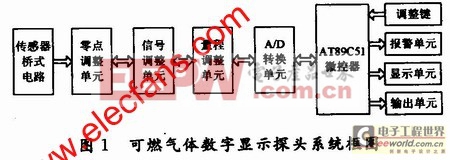
2 硬件电路设计
2.1 可燃气体传感器
经过试验对比,该设计采用半导体金属氧化物可燃气体传感器TGS842。这种具有高稳定性的传感器需要在一定的高温下工作,以实现其氧化还原反应,所以必须要有电压来为其加热,而加热电压是由+5 V的电源提供。该传感器的测量方式为:由其构成惠斯登检测桥路,当含有可燃性的混合气体扩散到检测元件上时,在气敏元件表面将会发生氧化还原反应,使电阻阻值发生变化,打破电桥平衡,产生大小与可燃气体浓度成正比的微小电压差信号,从而达到检测可燃气体浓度的目的。过程如图2所示。

2.2 信号调理电路
传感器输出的信号是微弱信号,需经过集成运算放大器OP07进行线性放大处理,以满足A/D转换电路对电平信号的要求。但在信号输入前,需加入一个具有 100个电阻值,并能对漂移信号进行精确调节的高精度数字电位器X9C103对输入漂移信号进行调零,使其不进入运算放大器OP07。具体流程为:电桥输出的信号一端经X9C103(P3.4控制)调零后;进入OP07的反相输入端(2脚),而输出电压V。则通过电阻R9接到反相输入端(2脚)和调零端(1脚)以保证引入的是负反馈;另一端由同相输入端(3脚)引入放大器,经放大后由另一个X9C103(P3.5控制)实现量程的外部调节。
信号经过2个数字电位器到达A/D转换单元。A/D转换单元由TLC549芯片实现,它以8位开关电容逐次逼近的方法实现转A/D转换。模拟信号有ANVIN引入,它通过,CLOCK和DATA OUT与AT89C51通信。当变为低电平后,TLC549芯片被选中,同时前次转换结果的最高有效位MSB(A7)自DATA OUT端输出。接着CLOCK端输出8个外部时钟信号,前7个CLOCK信号的作用是配合TLC549输出前次转换结果A6~A0,并为本次转换做准备。在第4个CLOCK信号由高变低后,片内采样保持电路对输入模拟量采样开始。第8个CLOCK信号的下降沿使片内采样保持电路进入保持状态,并启动A/D 开始转换。
为了使电路能够可靠稳定的工作,采用X5045实现电路监视功能。X5045有一个可设定200 ms,600 ms,1.4 s或禁止的看门狗定时器。在本电路中X5045被设置为1.4 s的定时器。硬件电路如图2所示,在单片机程序中,每隔一定的时间间隔放置一条“喂狗”指令(即在P1.6输出一个下降沿),该时间间隔应小于1.4 s,以保证程序正常运行时X5045不会溢出;当程序出现异常,该时间间隔将超过1.4 s导致X5045溢出,并通过RST引脚送出一个复位信号使单片机复位,重新开始运行程序。
2.3 输出单元
传感器的现场电压信号由电压/电流变换器转换成4~20 mA的标准电流信号后传送给上位机控制系统。为实现电压信号变换成4~20 mA标准电流信号,采用XTRl05精密电流变送器。它内含1个高精度的仪表放大器、1个电压/电流变换器和2个相同的O.8 mA精密恒流源基准。传感器的电压信号由13脚输入;3,4脚之间接滑动电阻以调节输出满幅值;1,2,14脚接电源,I/O脚接24 V电源正端(且是环流注入端);7脚通过负载电阻RL接电源负端(也是环流信号输出端);8,9脚外接BD235三极管,该三极管是4~20 mA电流回路的主要电流传导器件,能将外部电源电流与XTRl05的内部消耗严格地分开。
2.4 零点、量程调整及报警单元
本探头的量程为O~100%LEL,可针对不同环境对零点及量程做适当调整。按键电
- 基于DSP的信号采集处理系统(07-21)
- 基于DSP的视频采集存储系统的研究与设计 (06-04)
- 基于DSP CPLD信号采集系统通讯接口设计(01-12)
- 基于DSP核信号采集系统通讯接口电路设计(01-16)
- 基于DSP的继电保护测试仪信号采集系统硬件设计(03-20)
- 基于DSP核信号采集系统通讯接口设计(04-02)