通过虚拟现实对装甲越野车辆进行仿真和测试
时间:12-31
来源:互联网
点击:
传动系统模型范例
传动系统中的组件模型按照相关ECU的I/O要求,以不同的细节程度实现。从发动机的角度,基于地图的模型足以精确地描述发动机的行为。然而,喷油系统执行器要求提供从控制输入到位置传感器以及参数化的精确设备建模。
在本项目中,我们用实际喷油控制系统验证了此模型部分。对齿轮箱和扭矩变换器进行了物理建模,其中包含离合器和制动器模型,这些模型摩擦特性实现参数化。这使得齿轮更换,和换档期间的过渡行为,例如速度梯度和齿轮更换时间等建模都成为可能。这个步骤很有意义,因为凭借不同的制动器和离合器扭矩,齿轮箱执行器不仅可以以开/关方式,而且以中间步骤方式运行。,剩余传动系统模型包括了传动轴的弹性,因此它可以进行典型的传动系统振动。根据转向角度不同,每个车轮的曲线半径均不同,因此在转弯期间,传感器能够探测到各个车轮速度。
除了控制器输出信号之外,传动系统模型还处理制动系统模型所提供的制动扭矩,并将其运用到车轮上。传动系统的速度传感器输出为各个ECU提供支持,但由于它们的信号频率过高,很难由实时模型生成,而改由FPGA产生。模型只能提供通过传感器的轮齿的脉冲频率
所示模型在实时系统的一个处理器内核上运行,周期为0.1 ms。因此,模型所占的处理器内核计算资源不到20%。
试验自动化
为了充分利用HIL试验评台,我们需要一个灵活的的试验自动化环境。由于KMW 内部开发需要多种回归试验,出于质量和成本原因,自动化试验是必不可少的。
对于此应用,我们使用TraceTronic ECU-TEST的试验自动化环境。此工具用来指定、实施、执行和记录试验结果。
通过在相关试验环境中改变不同开发阶段的信号映射,试验案例的可重用性节约了用户的宝贵时间,试验采用可视化设计,无需编辑源代码。
ECU-TEST中实现的回归试验涵盖了所需验证水平的整个带宽,范围从模拟ECU输入和观察CAN上的相关响应等低水平试验,到故障管理和故障确认等相互作用及复杂功能的试验。这有助于将试验工作量降至先前工作量的15%,试验深度明显提升。
益处
生产先进、高度保护、相对轻质,并且具有多种新功能的多用途车辆只复杂的联网ECU来生产。车辆制造商负责整个系统,包含车辆、内部开发ECU,以及从外部供应商处获得的ECU。为了很好的完成任务,制造商会对所有的ECU进行集成和联合试验,确保它们能够一开始就正确地安装到车辆上。
新型的HIL试验平台是国际标准硬件与软件组件的独特组合。因此,客户可得到由HIL试验平台、定制实时模型和高度自动化试验环境所组成的定价优化、高度可扩展验证框架。此组合有助于制造商以高性价比的优化方式,集成不同的车辆ECU。由此客户也能够充分利用可扩展性和I/O灵活性的优势。凭借环路中的实时模型,AMPV的ECU网络能够快速验证,并提供优化整个系统的集成方法。在本项目中,与非HIL试验方法相比,此试验工作量减少了85%,同时试验深度明显提升。
结果
使用NI实时硬件和NI VeriStand软件,我们卓有成效地完成模型开发和HIL试验台集成。我们利用模型、试验台软件和硬件之间界限清晰的接口,并行执行所有三个领域的开发活动。NI VeriStand的简短学习曲线帮助我们快速建立与运行HIL试验系统。可扩展环境确保我们能够扩展HIL试验系统,以满足将来的需要。NI VeriStand的重新配置非常简便,这样当试验要求发生变化,例如,当信号和模型需要重新定线以进行调试时,可以更改配置。NI VeriStand与实时及FPGA硬件的固有集成使试验系统能够满足所需的定时要求,并能在将来进行试验扩展。
图1:这些装甲车辆超过现行防护标准,并实现良好的重量优化
图2:组合式HIL试验台
图3:系统示意图
图4:系统数据交换
图5:实时传动系统模型
欲了解此案例分析的更多信息,请联系:
René Müller
TraceTronic
电话: +49 (0) 351 – 20 57 68 27
传真: +49 (0) 351 – 20 57 68 99
Heidelberger Str. 24
01189德累斯顿
作者信息:
Andreas Abel
ITI
Webergasse 1 01067 Dresden
Dresden
德国
Tel: T +49 (0) 351 – 260 50 0
Fax: F +49 (0) 351 – 260 50 0
abel@itisim.com
传动系统中的组件模型按照相关ECU的I/O要求,以不同的细节程度实现。从发动机的角度,基于地图的模型足以精确地描述发动机的行为。然而,喷油系统执行器要求提供从控制输入到位置传感器以及参数化的精确设备建模。
在本项目中,我们用实际喷油控制系统验证了此模型部分。对齿轮箱和扭矩变换器进行了物理建模,其中包含离合器和制动器模型,这些模型摩擦特性实现参数化。这使得齿轮更换,和换档期间的过渡行为,例如速度梯度和齿轮更换时间等建模都成为可能。这个步骤很有意义,因为凭借不同的制动器和离合器扭矩,齿轮箱执行器不仅可以以开/关方式,而且以中间步骤方式运行。,剩余传动系统模型包括了传动轴的弹性,因此它可以进行典型的传动系统振动。根据转向角度不同,每个车轮的曲线半径均不同,因此在转弯期间,传感器能够探测到各个车轮速度。
除了控制器输出信号之外,传动系统模型还处理制动系统模型所提供的制动扭矩,并将其运用到车轮上。传动系统的速度传感器输出为各个ECU提供支持,但由于它们的信号频率过高,很难由实时模型生成,而改由FPGA产生。模型只能提供通过传感器的轮齿的脉冲频率
所示模型在实时系统的一个处理器内核上运行,周期为0.1 ms。因此,模型所占的处理器内核计算资源不到20%。
试验自动化
为了充分利用HIL试验评台,我们需要一个灵活的的试验自动化环境。由于KMW 内部开发需要多种回归试验,出于质量和成本原因,自动化试验是必不可少的。
对于此应用,我们使用TraceTronic ECU-TEST的试验自动化环境。此工具用来指定、实施、执行和记录试验结果。
通过在相关试验环境中改变不同开发阶段的信号映射,试验案例的可重用性节约了用户的宝贵时间,试验采用可视化设计,无需编辑源代码。
ECU-TEST中实现的回归试验涵盖了所需验证水平的整个带宽,范围从模拟ECU输入和观察CAN上的相关响应等低水平试验,到故障管理和故障确认等相互作用及复杂功能的试验。这有助于将试验工作量降至先前工作量的15%,试验深度明显提升。
益处
生产先进、高度保护、相对轻质,并且具有多种新功能的多用途车辆只复杂的联网ECU来生产。车辆制造商负责整个系统,包含车辆、内部开发ECU,以及从外部供应商处获得的ECU。为了很好的完成任务,制造商会对所有的ECU进行集成和联合试验,确保它们能够一开始就正确地安装到车辆上。
新型的HIL试验平台是国际标准硬件与软件组件的独特组合。因此,客户可得到由HIL试验平台、定制实时模型和高度自动化试验环境所组成的定价优化、高度可扩展验证框架。此组合有助于制造商以高性价比的优化方式,集成不同的车辆ECU。由此客户也能够充分利用可扩展性和I/O灵活性的优势。凭借环路中的实时模型,AMPV的ECU网络能够快速验证,并提供优化整个系统的集成方法。在本项目中,与非HIL试验方法相比,此试验工作量减少了85%,同时试验深度明显提升。
结果
使用NI实时硬件和NI VeriStand软件,我们卓有成效地完成模型开发和HIL试验台集成。我们利用模型、试验台软件和硬件之间界限清晰的接口,并行执行所有三个领域的开发活动。NI VeriStand的简短学习曲线帮助我们快速建立与运行HIL试验系统。可扩展环境确保我们能够扩展HIL试验系统,以满足将来的需要。NI VeriStand的重新配置非常简便,这样当试验要求发生变化,例如,当信号和模型需要重新定线以进行调试时,可以更改配置。NI VeriStand与实时及FPGA硬件的固有集成使试验系统能够满足所需的定时要求,并能在将来进行试验扩展。
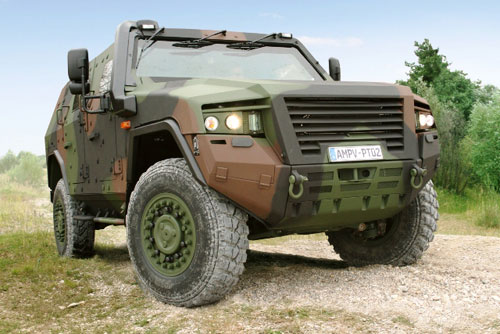
图1:这些装甲车辆超过现行防护标准,并实现良好的重量优化
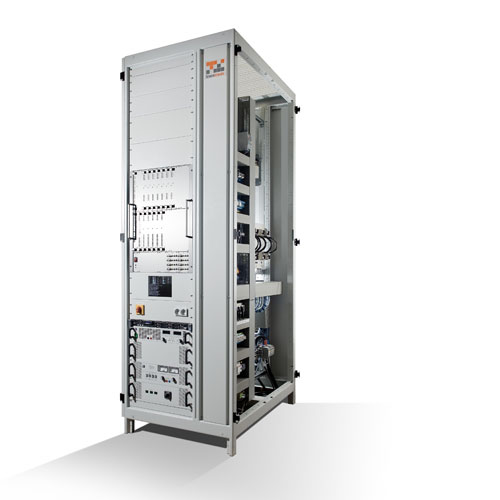
图2:组合式HIL试验台
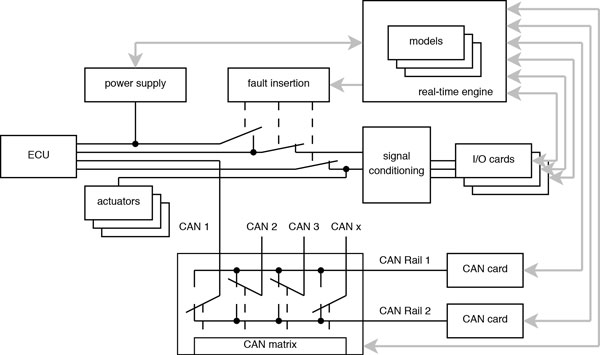
图3:系统示意图

图4:系统数据交换
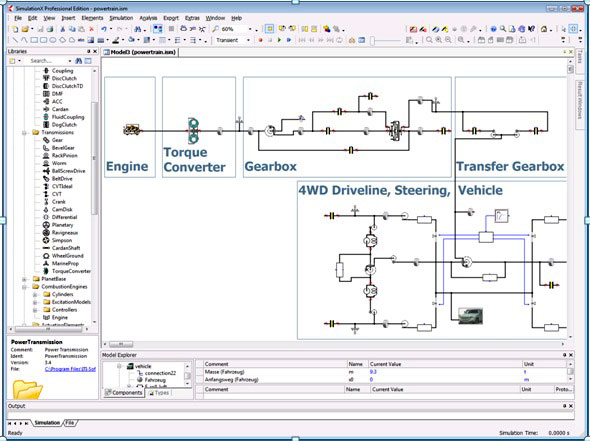
图5:实时传动系统模型
欲了解此案例分析的更多信息,请联系:
René Müller
TraceTronic
电话: +49 (0) 351 – 20 57 68 27
传真: +49 (0) 351 – 20 57 68 99
Heidelberger Str. 24
01189德累斯顿
作者信息:
Andreas Abel
ITI
Webergasse 1 01067 Dresden
Dresden
德国
Tel: T +49 (0) 351 – 260 50 0
Fax: F +49 (0) 351 – 260 50 0
abel@itisim.com
仿真 嵌入式 电子 PXI 传感器 FPGA LabVIEW 电压 显示器 自动化 相关文章:
- 在采用FPGA设计DSP系统中仿真的重要性 (06-21)
- 数字频率合成器的FPGA实现(08-07)
- 基于DSP的导弹仿真器嵌入式组件设计(04-30)
- 如何将DSP和MCU两者完美结合(08-10)
- 高性能仿真器与开发包加速普及DSP应用开发(11-22)
- 基于DSP内嵌PCI总线的卫星信号仿真器设计(04-17)