克服汽车系统中高亮度(HB) LED集成方案的技术瓶颈
时间:12-01
来源:互联网
点击:
传统多串LED驱动器的问题
传统的多串LED驱动器方案采用图2所示拓扑,包含boost开关转换器和多路独立工作的吸电流调节器,使用这些驱动器构建AVO时,需要一些外部元件,这会引起一系列的问题。
其中一个问题是:外部电路必须检测哪一串LED具有最高的正向导通电压(或最低的阴极电压);利用图2中红色标记的几个二极管可以实现这一功能。这种方案会占用更大的电路板面积,增加系统成本。
该方案在出现LED故障时还存在另一潜在问题,如果一个LED失效发生开路,这一串的阴极电压将跌落至零,二极管检测电路将判断这一串具有最高的正向导通电压,并开始提升VBOOST,试图为这一串LED提供足够的驱动电压。这将引出几个潜在问题,提升后的电压作用在其它串的吸电流MOSFET上,可能造成全部管子失效;或者,电压的提升将触发boost转换器的输出过压保护(OVP),如果器件具有此项功能,则关闭转换器和所有LED串。
该架构的第三个问题是LED的PWM调光,当LED关闭时,二极管电路没有电压参考点来设置VBOOST。一种可能的解决办法是增加另一个二极管,通过分压电路连接到boost输出,如图2中的红色标记电路。LED关闭时,该二极管导通,将VBOOST设置到预置电压。这种方式存在的显著问题是:进行PWM调光时,boost转换器的输出电压具有较高的纹波,纹波频率为PWM调光频率(见图3)。电压纹波会产生EMI噪声,如上所述,这是汽车设计面临的一个关键问题,它还会从输出电容COUT上产生音频噪声。
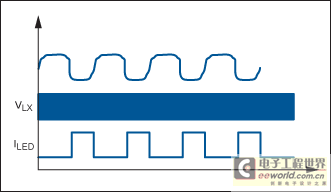
图3a. 传统驱动器进行PWM调光时的波形,利用图2所示外部电路,VBOOST在LED电流通、断期间发生变化,电源上存在较大噪声。
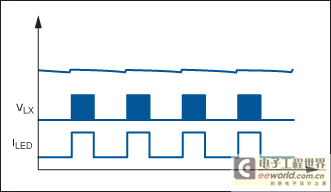
图3b. 在新一代驱动器架构中,boost转换器在LED电流断开期间停止开关工作,转换器输出电压由其输出电容保持,由于漏电流的作用,电压略有下降。
新一代多串LED驱动器的优势
新一代多串LED驱动器在性能上有较大改进,boost开关转换器与线性吸电流调节器部分可以进行双向通信,而不是独立工作。因此,新型多串驱动器解决了上述三个问题。
这些新型驱动器在IC内部检测LED串的电压,即每个吸电流MOSFET的漏极电压,IC利用内部二极管或模拟开关电路选择最低串电压(图4)。这种方案大大降低了外部元件数量和方案成本。
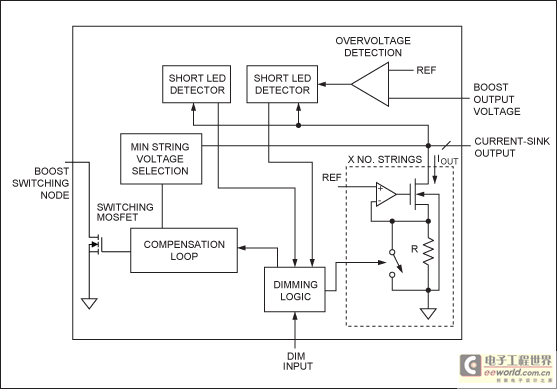
图4. 新一代HB LED驱动器IC中,内部LED吸电流调节器与boost转换器之间的通信功能有助于获得更高效率,避免了许多传统驱动器所面临的问题。
另外,双向通信功能还解决了上述一个LED失效或开路引发的问题,新设计中一旦一个LED发生故障,VBOOST开始上升,电压达到OVP门限时即可识别出发生故障的串,从AVO控制环路中禁止或移出该串,其它LED串保持正常工作。除了降低照明亮度外(而不是全部关闭LED),不会对用户造成其它影响。
通过PWM调节LED亮度时,需要考虑LED驱动器开关操作的几个因素。集成开关和线性调节环路采用了与图2不同的方式,具有更低噪声。LED关闭时,新型boost转换器可禁止工作,如图3b所示。如果转换器在此期间停止了开关操作,功率开关MOSFET将保持在断开状态,补偿电路也处于开路。此时,补偿电容保持其电荷量,这是补偿环路的状态。VBOOST由输出电容COUT维持,由于LED关闭电容不会放电,COUT的放电电流只是漏电流。LED恢复导通时,转换器重新启动开关操作,具有极小纹波。这种方案中,VBOOST在PWM亮度调节期间几乎保持恒定,大大降低了EMI噪声和输出电容产生的音频噪声。
这种方案的唯一限制是PWM调光的导通周期需要大于几个(例如:三个或四个)开关周期,以便boost转换器为COUT重新充电,补偿关断期间的漏电流损耗。这限制了能够获得的最小占空比。
新一代驱动器应用
汽车的日间行驶灯和平视显示器具有一个相同的性能要求:在汽车行驶过程中始终保持开启状态,要求较高的可靠性/冗余设计,任何情况下确保正常工作。利用MAX16814等新一代多串驱动器能够保证行驶灯和平视显示器高度可靠,同时还大大减少了外部元件的数量。较少的元件数量降低了故障概率,有助于提高系统可靠性,降低系统成本。
这类涉及人身安全的应用还具有一些类似要求:工作在较宽的输入电压范围,能够承受典型值高达40V的汽车电池峰值电压(抛负载)并具有极低的EMI。
故障容限是一个关键考虑因素,即使在发生故障时也不允许关闭LED灯,这一点非常重要。MAX16814利用多串驱动架构能够在出现一个LED开路或短路时只关闭出现故障的LED串,其它LED保持有效工作。此外,MAX16814的故障指示输出还可以提供LED失效报警(图5)。
平视显示器还要求较宽(1000:1或更大)的PWM调光范围,MAX16814集成了一个独特的PWM调光电路,能够有效抑制VBOOST的纹波(频率为调光频率),从而降低了EMI和可闻噪声。该MAX16814方案与图3b使用的方案类似,但能够以200Hz提供5000:1的超宽PMW调光范围,这一调光范围高于任何同类产品,克服了上述最小导通时间的限制。
MAX16814可以驱动4串LED,每串电流可达150mA,开关和线性调节器之间可进行双向通信。该芯片大大减少了外部元件的数量。另外,MAX16814具有完备的故障保护措施和检测功能,任何一串出现开路或短路的LED时将关闭这一串的工作,并向系统发出故障报警输出。此外,该IC 满足汽车产品设计的所有要求,可承受40V抛负载,工作在-40°C至+125°C温度范围。
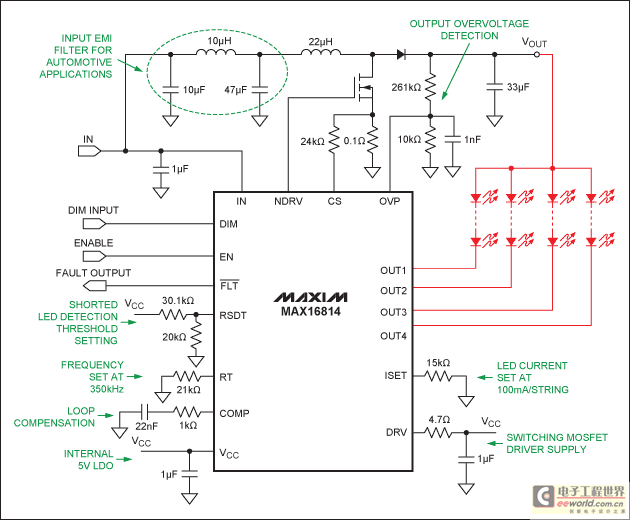
图5. 这是一个完整的汽车平视显示器或行驶灯驱动子系统的设计案例,电路包含了所有外部元件和输入EMI滤波器,借助MAX16814的低噪声特性,外部EMI滤波元件值可以很小。
设计HB LED系统时需要折衷考虑多方面因素,例如:元件数量、效率、可靠性等。表1对多种LED驱动方案进行了对比和归纳,有助于设计人员针对具体应用选择最佳方案。
表1. HB LED驱动方案总结
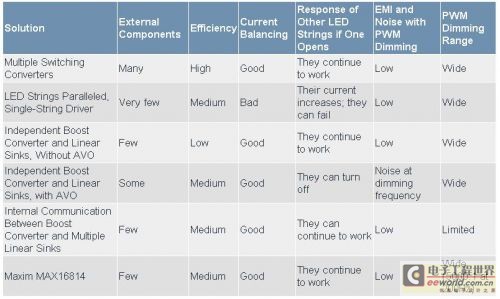
新一代LED驱动器大大减少了外部元件数量,此外,利用开关电路与线性调整电路之间的双向通信能够实现高性价比方案,具有更高效率,并有效改善系统性能,包括:故障保护与检测。MAX16814是一款多串驱动器,具有上述所有优势,PWM调光范围高于市场上任何类似产品。
传统的多串LED驱动器方案采用图2所示拓扑,包含boost开关转换器和多路独立工作的吸电流调节器,使用这些驱动器构建AVO时,需要一些外部元件,这会引起一系列的问题。
其中一个问题是:外部电路必须检测哪一串LED具有最高的正向导通电压(或最低的阴极电压);利用图2中红色标记的几个二极管可以实现这一功能。这种方案会占用更大的电路板面积,增加系统成本。
该方案在出现LED故障时还存在另一潜在问题,如果一个LED失效发生开路,这一串的阴极电压将跌落至零,二极管检测电路将判断这一串具有最高的正向导通电压,并开始提升VBOOST,试图为这一串LED提供足够的驱动电压。这将引出几个潜在问题,提升后的电压作用在其它串的吸电流MOSFET上,可能造成全部管子失效;或者,电压的提升将触发boost转换器的输出过压保护(OVP),如果器件具有此项功能,则关闭转换器和所有LED串。
该架构的第三个问题是LED的PWM调光,当LED关闭时,二极管电路没有电压参考点来设置VBOOST。一种可能的解决办法是增加另一个二极管,通过分压电路连接到boost输出,如图2中的红色标记电路。LED关闭时,该二极管导通,将VBOOST设置到预置电压。这种方式存在的显著问题是:进行PWM调光时,boost转换器的输出电压具有较高的纹波,纹波频率为PWM调光频率(见图3)。电压纹波会产生EMI噪声,如上所述,这是汽车设计面临的一个关键问题,它还会从输出电容COUT上产生音频噪声。
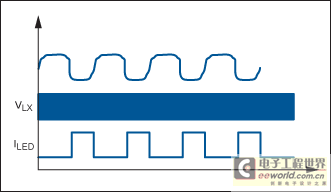
图3a. 传统驱动器进行PWM调光时的波形,利用图2所示外部电路,VBOOST在LED电流通、断期间发生变化,电源上存在较大噪声。
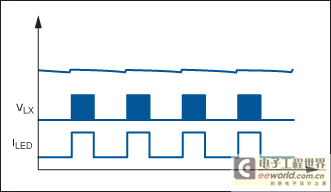
图3b. 在新一代驱动器架构中,boost转换器在LED电流断开期间停止开关工作,转换器输出电压由其输出电容保持,由于漏电流的作用,电压略有下降。
新一代多串LED驱动器的优势
新一代多串LED驱动器在性能上有较大改进,boost开关转换器与线性吸电流调节器部分可以进行双向通信,而不是独立工作。因此,新型多串驱动器解决了上述三个问题。
这些新型驱动器在IC内部检测LED串的电压,即每个吸电流MOSFET的漏极电压,IC利用内部二极管或模拟开关电路选择最低串电压(图4)。这种方案大大降低了外部元件数量和方案成本。
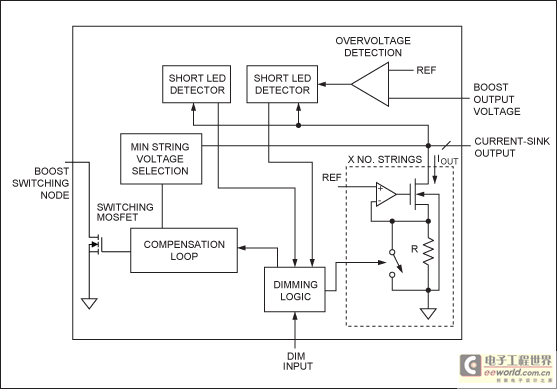
图4. 新一代HB LED驱动器IC中,内部LED吸电流调节器与boost转换器之间的通信功能有助于获得更高效率,避免了许多传统驱动器所面临的问题。
另外,双向通信功能还解决了上述一个LED失效或开路引发的问题,新设计中一旦一个LED发生故障,VBOOST开始上升,电压达到OVP门限时即可识别出发生故障的串,从AVO控制环路中禁止或移出该串,其它LED串保持正常工作。除了降低照明亮度外(而不是全部关闭LED),不会对用户造成其它影响。
通过PWM调节LED亮度时,需要考虑LED驱动器开关操作的几个因素。集成开关和线性调节环路采用了与图2不同的方式,具有更低噪声。LED关闭时,新型boost转换器可禁止工作,如图3b所示。如果转换器在此期间停止了开关操作,功率开关MOSFET将保持在断开状态,补偿电路也处于开路。此时,补偿电容保持其电荷量,这是补偿环路的状态。VBOOST由输出电容COUT维持,由于LED关闭电容不会放电,COUT的放电电流只是漏电流。LED恢复导通时,转换器重新启动开关操作,具有极小纹波。这种方案中,VBOOST在PWM亮度调节期间几乎保持恒定,大大降低了EMI噪声和输出电容产生的音频噪声。
这种方案的唯一限制是PWM调光的导通周期需要大于几个(例如:三个或四个)开关周期,以便boost转换器为COUT重新充电,补偿关断期间的漏电流损耗。这限制了能够获得的最小占空比。
新一代驱动器应用
汽车的日间行驶灯和平视显示器具有一个相同的性能要求:在汽车行驶过程中始终保持开启状态,要求较高的可靠性/冗余设计,任何情况下确保正常工作。利用MAX16814等新一代多串驱动器能够保证行驶灯和平视显示器高度可靠,同时还大大减少了外部元件的数量。较少的元件数量降低了故障概率,有助于提高系统可靠性,降低系统成本。
这类涉及人身安全的应用还具有一些类似要求:工作在较宽的输入电压范围,能够承受典型值高达40V的汽车电池峰值电压(抛负载)并具有极低的EMI。
故障容限是一个关键考虑因素,即使在发生故障时也不允许关闭LED灯,这一点非常重要。MAX16814利用多串驱动架构能够在出现一个LED开路或短路时只关闭出现故障的LED串,其它LED保持有效工作。此外,MAX16814的故障指示输出还可以提供LED失效报警(图5)。
平视显示器还要求较宽(1000:1或更大)的PWM调光范围,MAX16814集成了一个独特的PWM调光电路,能够有效抑制VBOOST的纹波(频率为调光频率),从而降低了EMI和可闻噪声。该MAX16814方案与图3b使用的方案类似,但能够以200Hz提供5000:1的超宽PMW调光范围,这一调光范围高于任何同类产品,克服了上述最小导通时间的限制。
MAX16814可以驱动4串LED,每串电流可达150mA,开关和线性调节器之间可进行双向通信。该芯片大大减少了外部元件的数量。另外,MAX16814具有完备的故障保护措施和检测功能,任何一串出现开路或短路的LED时将关闭这一串的工作,并向系统发出故障报警输出。此外,该IC 满足汽车产品设计的所有要求,可承受40V抛负载,工作在-40°C至+125°C温度范围。
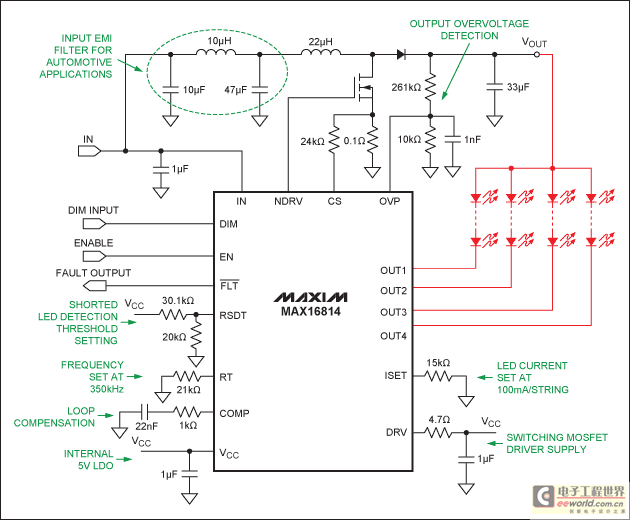
图5. 这是一个完整的汽车平视显示器或行驶灯驱动子系统的设计案例,电路包含了所有外部元件和输入EMI滤波器,借助MAX16814的低噪声特性,外部EMI滤波元件值可以很小。
设计HB LED系统时需要折衷考虑多方面因素,例如:元件数量、效率、可靠性等。表1对多种LED驱动方案进行了对比和归纳,有助于设计人员针对具体应用选择最佳方案。
表1. HB LED驱动方案总结
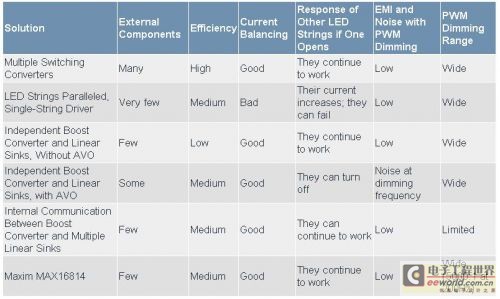
新一代LED驱动器大大减少了外部元件数量,此外,利用开关电路与线性调整电路之间的双向通信能够实现高性价比方案,具有更高效率,并有效改善系统性能,包括:故障保护与检测。MAX16814是一款多串驱动器,具有上述所有优势,PWM调光范围高于市场上任何类似产品。
LED 显示器 PWM PCB 电路 电容 电流 电压 电感 MOSFET 二极管 滤波器 相关文章:
- 基于超声波检测的倒车雷达设计(11-28)
- 另类传感器观念:汽车传感器(11-30)
- RGB色彩传感器工作原理及应用方案分析(上)(01-04)
- RGB色彩传感器工作原理及应用方案分析(下)(01-04)
- 凌特LT3474 LED驱动器利用汽车电源给高亮度LED供电(01-12)
- 高压、可调恒流LED驱动器MAX16800及其应用(02-19)