基于TMS320F2812的双通道高精度伺服系统
时间:11-27
来源:互联网
点击:
3 控制策略及实现
本系统为实时性强的数字化高精度伺服系统。在系统设计中,充分利用了数字控制技术,简化硬件电路设计,提高系统可靠性,充分发挥软件强大功能,用软件产生部分传统上由硬件电路实现的功能。控制器软件主要由两个部分构成,一是主循环程序,二是PWM定时器下溢中断服务子程序。主程序和中断服务子程序相互配合,完成伺服电机的实时控制。主循环程序负责硬件外设的初始化、数据初始化和电机工作状态转换,并在发生故障时产生报警信息。由于采用的是单芯片控制两台伺服电机的方法,因此实现两台伺服电机的协同控制,完成状态机的切换是主程序最重要的任务。按照设备的工作要求,两台伺服电机分为左右电机,其工作状态有5个:左电机单独工作、右电机单独工作、左右电机同步工作、左右电机差动工作和左右电机锁定保持,其中左/右电机单独工作时,另外一台电机处于锁定状态,防止误动作。根据上位机发送的控制指令,主程序确定工作状态,为中断服务子程序的控制实现做准备。PWM定时器下溢中断服务子程序是核心部分,实现旋转变压器信号读取、电流检测、电压检测、转速计算和系统闭环控制等功能。TMS320F2812 集成有两个事件管理器,每个事件管理器可以单独控制一台伺服电机。由于硬件电路采用了相同的设计,伺服电机完全相同,最后的技术指标也一致,因此对两台伺服电机的控制采取相同的控制算法,分别由各个事件管理器的中断服务子程序调用执行。根据SVPWM算法原理,在TMS320F2812中存储了一个正弦表格,表格的长度依据旋转变压器的分辨率和系统要求的控制精度进行设置。由于采用了高精度的旋转变压器实现位置检测,根据测得的无刷直流电动机反电势信号将一个电周期划分为六个扇区,由读取的旋转变压器信号确定相应的扇区号。图4是PWM定时器中断服务子程序的流程图。
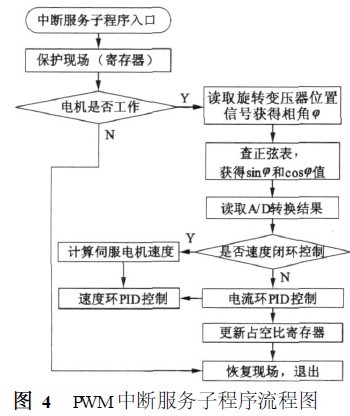
在PWM中断服务子程序中,实时读取RDC电路的输出信号,作为SVPWM控制算法的角度依据; RDC电路的输出信号与电机转子位置信息相对应,可计算出伺服系统的转速和位置信号,并根据A /D采样获得的电流信号,计算实时误差,实现系统闭环控制,产生新的PWM占空比,通过调节占空比,控制作为伺服驱动单元的无刷直流电动机的转速,达到实现伺服系统高精度控制的目的。
4 实验结果与结论
伺服系统采用的两台无刷直流电动机实验样机主要参数为:额定功率80W,额定电压28 V,最高转速1 500 r/min,极对数p = 2,相电阻R = 0. 42Ω,相电感L = 2. 1 mH。系统工作时的PWM斩波频率为25 kHz, SVPWM采用双极性调制技术。
图5a是左右通道经过RC滤波后的一相电压波形,图5b是单台伺服电机工作时的相电流波形,图5c是伺服系统的起动加速曲线。采用软起动方式初始加速时间稍长,但对伺服系统具有一定的保护功能;并且系统采用了软起动技术,使得在加速阶段转速超调几乎为零,保证了系统的精度。系统运行在最高转速时,在10 min内测量到的最大角度误差为1. 87°,而最大转速偏差为±1. 0%。由于采用了高精度的旋转变压器作为检测元件,伺服系统的最低转速低至0. 1r /min,满足了低速场合的要求。实验结果表明,利用TMS320F2812同时控制两台伺服电机,利用合理的控制算法和高精度传感器,能够获得较高的控制精度,满足设计目标的要求。
本系统为实时性强的数字化高精度伺服系统。在系统设计中,充分利用了数字控制技术,简化硬件电路设计,提高系统可靠性,充分发挥软件强大功能,用软件产生部分传统上由硬件电路实现的功能。控制器软件主要由两个部分构成,一是主循环程序,二是PWM定时器下溢中断服务子程序。主程序和中断服务子程序相互配合,完成伺服电机的实时控制。主循环程序负责硬件外设的初始化、数据初始化和电机工作状态转换,并在发生故障时产生报警信息。由于采用的是单芯片控制两台伺服电机的方法,因此实现两台伺服电机的协同控制,完成状态机的切换是主程序最重要的任务。按照设备的工作要求,两台伺服电机分为左右电机,其工作状态有5个:左电机单独工作、右电机单独工作、左右电机同步工作、左右电机差动工作和左右电机锁定保持,其中左/右电机单独工作时,另外一台电机处于锁定状态,防止误动作。根据上位机发送的控制指令,主程序确定工作状态,为中断服务子程序的控制实现做准备。PWM定时器下溢中断服务子程序是核心部分,实现旋转变压器信号读取、电流检测、电压检测、转速计算和系统闭环控制等功能。TMS320F2812 集成有两个事件管理器,每个事件管理器可以单独控制一台伺服电机。由于硬件电路采用了相同的设计,伺服电机完全相同,最后的技术指标也一致,因此对两台伺服电机的控制采取相同的控制算法,分别由各个事件管理器的中断服务子程序调用执行。根据SVPWM算法原理,在TMS320F2812中存储了一个正弦表格,表格的长度依据旋转变压器的分辨率和系统要求的控制精度进行设置。由于采用了高精度的旋转变压器实现位置检测,根据测得的无刷直流电动机反电势信号将一个电周期划分为六个扇区,由读取的旋转变压器信号确定相应的扇区号。图4是PWM定时器中断服务子程序的流程图。
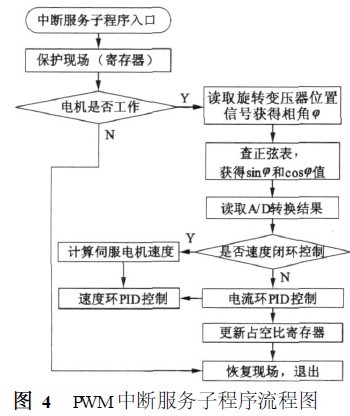
在PWM中断服务子程序中,实时读取RDC电路的输出信号,作为SVPWM控制算法的角度依据; RDC电路的输出信号与电机转子位置信息相对应,可计算出伺服系统的转速和位置信号,并根据A /D采样获得的电流信号,计算实时误差,实现系统闭环控制,产生新的PWM占空比,通过调节占空比,控制作为伺服驱动单元的无刷直流电动机的转速,达到实现伺服系统高精度控制的目的。
4 实验结果与结论
伺服系统采用的两台无刷直流电动机实验样机主要参数为:额定功率80W,额定电压28 V,最高转速1 500 r/min,极对数p = 2,相电阻R = 0. 42Ω,相电感L = 2. 1 mH。系统工作时的PWM斩波频率为25 kHz, SVPWM采用双极性调制技术。
图5a是左右通道经过RC滤波后的一相电压波形,图5b是单台伺服电机工作时的相电流波形,图5c是伺服系统的起动加速曲线。采用软起动方式初始加速时间稍长,但对伺服系统具有一定的保护功能;并且系统采用了软起动技术,使得在加速阶段转速超调几乎为零,保证了系统的精度。系统运行在最高转速时,在10 min内测量到的最大角度误差为1. 87°,而最大转速偏差为±1. 0%。由于采用了高精度的旋转变压器作为检测元件,伺服系统的最低转速低至0. 1r /min,满足了低速场合的要求。实验结果表明,利用TMS320F2812同时控制两台伺服电机,利用合理的控制算法和高精度传感器,能够获得较高的控制精度,满足设计目标的要求。
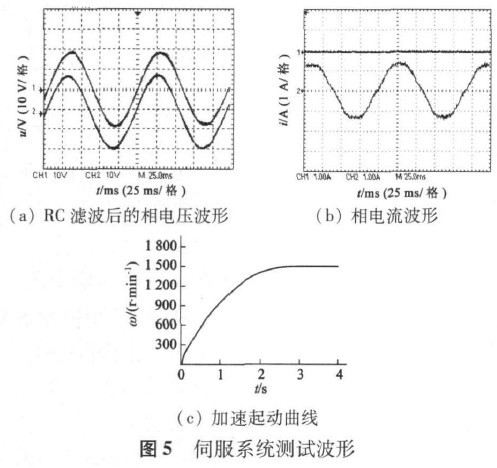
电动机 电子 自动化 电压 PWM 电感 传感器 变压器 总线 电路 信号发生器 MOSFET 电流 二极管 逆变器 放大器 电阻 集成电路 相关文章:
- 基于ARM微处理器LPC2132的智能电动机保护器设计(07-23)
- 基于ATmega8的大功率直流电机控制系统设计与实现(09-20)
- Atmega16在开关磁阻电机调速系统中的应用(06-08)
- DSP芯片介绍及其选型(06-07)
- 基于单片机AT89C51的时间/位移换向控制器设计(06-13)
- 单片机在电动机保护中的应用(07-23)