直线电机的转子设计方案
0 引言
数控机床正在向高精密、高速、高复合、高智能和环保的方向发展。高精密和高速加工对传动及其控制提出了更高的要求:更高的动态特性和控制精度,更高的进给速度和加速度,更低的振动噪声和更小的磨损。在传统的传动链中,作为动力源的电动机要通过齿轮、蜗轮副,皮带、丝杠副、联轴器、离合器等中间传动环节才能将动力送达工作部件。在这些环节中产生了较大的转动惯量、弹性变形、反向间隙、运动滞后、摩擦、振动、噪声及磨损。虽然在这些方面通过不断的改进使传动性能有所提高,但问题很难从根本上解决,于是出现了“直接传动”的概念,即取消从电动机到工作部件之间的各种中间环节。随着电机及其驱动控制技术的发展,电主轴、直线电机、力矩电机的出现和技术的日益成熟,使主轴、直线和旋转坐标运动的“直接传动”概念变为现实,并日益显示出巨大的优越性。直线电机及其驱动控制技术在机床进给驱动上的应用,使机床的传动结构出现了重大变化,并使机床性能有了新的飞跃。
1 直线电机
1.1 直线电机工作原理
所谓线性马达又称为直线电机,是一种将传统的旋转电机沿轴线方向切开后,将旋转电机的初级展开作为直线电机(线性马达)的定子,次级通电后在电磁力的作用下沿着初级做直线运动,称为直线电机(线性马达)的转子,如图1所示。直线电机作为一种传动装置,能够将电能直接转换成直线运动机械能,而不需要任何中间转换机构。
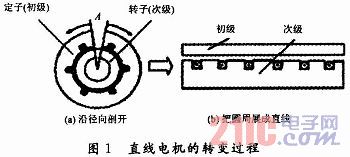
1.2 直线电机的特点
根据直线电机概念、原理,认识直线电机应把握以下特点:
(1)进给速度范围宽。可覆盖从1 mm/s~20 m/min以上的速度范围,目前加工中心的快进速度已达208 m/min,而传统机床快进速度小于60 m/min,一般为20~30 m/min。
(2)速度特性好。速度偏差可达0.01%以下,加速度大,直线电机最大加速度可达30 g,目前加工中心的进给加速度已达3.24 g,激光加工机给加速度已达5 g,而传统机床进给加速度在1 g以下,一般为0.3 g。
(3)定位精度高。采用光栅闭环控制,定位精度可达0.1~0.01 mm。应用前馈控制的直线电机驱动系统可减少跟踪误差200倍以上。由于运动部件的动态特性好,响应灵敏,加上插补控制的精细化,可实现纳米级控制。
(4)行程不受限制。传统的丝杠传动受丝杠制造工艺限制,一般为4~6 m,更长的行程需要接长丝杠,无论从制造工艺还是在性能上都不理想。而采用直线电机驱动,定子可无限加长,且制造工艺简单,已有大型高速加工中心x轴长达40 m以上。另外,直线电机还具有结构简单、运动平稳、噪声小、运动部件摩擦小、磨损小、使用寿命长、安全可靠等优点。
2 直线电机的驱动控制技术
一个直线电机应用系统不仅是性能良好的直线电机,还必须是能在安全可靠的条件下实现技术与经济要求的控制系统。随着自动控制技术与微计算机技术的发展,直线电机的控制方法越来越多。对直线电机控制技术的研究基本上可以分为三个方面:一是传统控制技术,二是现代控制技术,三是智能控制技术。
传统的控制技术如PID反馈控制、解耦控制等在交流伺服系统中得到了广泛的应用。其中PID控制蕴涵动态控制过程中的过去、现在和未来的信息,而且配置几乎为最优,具有较强的鲁棒性,是交流伺服电机驱动系统中最基本的控制方式。为了提高控制效果,往往采用解耦控制和矢量控制技术。
在对象模型确定、不变化且是线性的以及操作条件、运行环境是确定不变的条件下,采用传统控制技术是简单有效的。但是在高精度微进给的高性能场合,就必须考虑对象结构与参数的变化。各种非线性的影响,运行环境的改变及环境干扰等时变和不确定因数,才能得到满意的控制效果。因此,现代控制技术在直线伺服电机控制的研究中引起了很大的重视。常用控制方法有自适应控制、滑模变结构控制、鲁棒控制及智能控制。
近年来模糊逻辑控制、神经网络控制等智能控制方法也被引入直线电动机驱动系统的控制中。目前主要是将模糊逻辑、神经网络与PID、H∞控制等
电动机直线电机数控机 相关文章:
- Windows CE 进程、线程和内存管理(11-09)
- RedHatLinux新手入门教程(5)(11-12)
- uClinux介绍(11-09)
- openwebmailV1.60安装教学(11-12)
- Linux嵌入式系统开发平台选型探讨(11-09)
- Windows CE 进程、线程和内存管理(二)(11-09)