埋嵌式元件共面度测量方法研究(一)
1 背景
随着电子行业朝高功率、微型化、组件高密度集中化方向的快速发展,电子产品的功率密度越来越大,体积越来越小,如何寻求和优化最佳散热方法及其结构设计,成为当今电子工业设计的一个巨大的挑战。有研究表明,电子元器件工作温度在(70~80)℃范围内每升高1 ℃,其可靠性将下降5%.因此对于PCB行业来说,开发PCB散热管理技术,降低PCB工作温度,是提高PCB及其系统的可靠性的重要途径。
早在1985年,在日本电气化学工业株式会社就问世了第一代的散热基板产品“HITTv[g”(HITT板块散热)。目前PCB市场上出现的超厚铜箔板材、导热板材、金属基板(铜基板、铝基板)、夹铜芯板和埋嵌金属块板等散热管理相关产品,就是电子行业研发工作者聪明才智和辛勤劳动的结晶。
所谓埋嵌金属块板(图1),是在PCB板上对应贴装高功率元器件局部位置埋嵌金属块(紫铜块或铝块),客户端使用时高功率元器件直接贴装到金属块上面,器件工作时产生的大量热量通过金属块传导到PCB另外一侧的专用散热器件上,从而有效降低元器件和PCB工作温度,提高设备使用寿命。可见,包含埋嵌式器件的PCB技术的开发,可有效促进PCB高密化发展、提高PCB组装可靠性、改善电子互连电气性能,同时相对常规金属基板又节省了成本,是一项前途光明的先进技术。
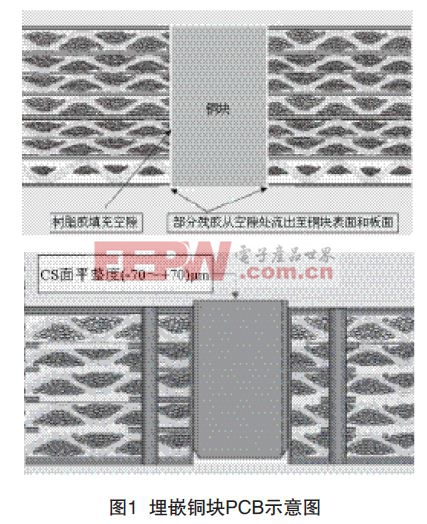
共面度(Coplanarity)是表征诸多被测对象与样品基准面之间的偏移量的指标,对于PCB行业而言,更为常见的类似定义是平面度和翘曲度,共面度、平面度和翘曲度三者的区别和相似点分析如表1 所示。
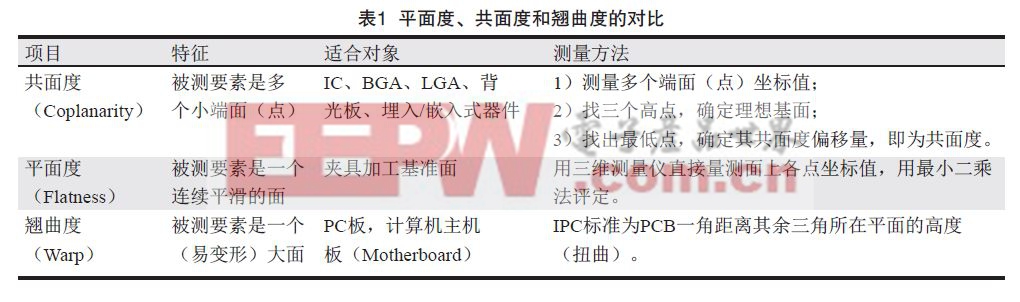
由表1可见,对于常规PCB而言,翘曲度是关键指标。而对于含埋嵌式元件PCB而言,更为重要的是局部位置(埋嵌元件位置)内各器件的共面度。共面度、平面度和翘曲度三者的共同点是,反映样品的实际状况相对理想状态的变动量。
由于客户需要在PCB埋嵌元件表面贴装、焊接高功率元器件和散热器件,如器件与PCB共面度不佳,则容易缺锡膏导致功率器件或散热器件焊接不牢,或锡膏过多导致高功率元器件短路。因此在埋嵌元件PCB制作过程中,必须严格控制和监测埋嵌元件与PCB的共面度。
2 现状分析
当前PCB行业内对埋嵌元件共面度的测量方法没有统一和明确的规范,但在PCBA贴装和焊接过程,则对焊脚相对PCB表面的共面度有控制要求(图2)。
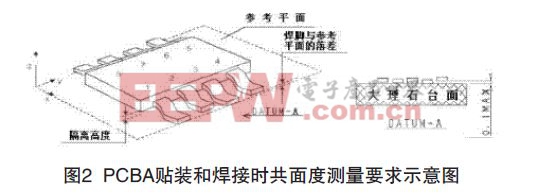
在此需要定义几个测量共面度过程中的关键术语:
(1)共面度:反映诸多被测对象与样品基准面之间的偏移量。
(2)共面度偏移量:被测对象与样品基准面之间的距离。
(3)共面度最终测量值就是所有被测对象的共面度偏移量的最大值。
常规的测量共面度方法有两种:三棱镜法(图3)和投影法(图4)。一般来说,三棱镜法可以测量样品五个表面所有被测点与基准面之间的距离,而投影法仅可测量样品投影表面(1个表面)被测点与基准面之间的距离。两种方法的测量原理相同,因此测量精度也完全相同,但投影法测量速度比三棱镜法快3倍以上。
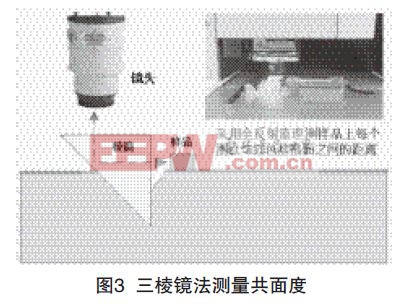
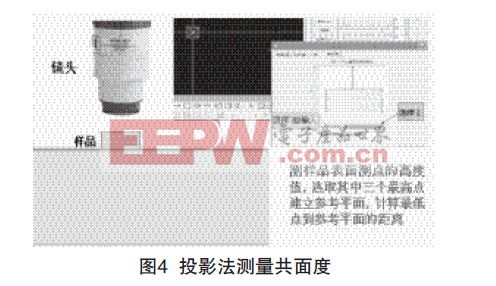
上述两种方法都需要专用的三维扫描测量仪器,且行业内还没有成熟的将其用于测量PCB内埋嵌元件共面度的经验。因此,开发和完善对于PCB内埋嵌铜块共面度的检测方法,具有十分重要的意义。
3 共面度检测方法对比
综合考察PCB及相关上下游行业对共面度/平面度的测量需求,有金相切片分析法、三维坐标仪测量法、三维影像测量法以及接触式三维坐标仪测量法等较常用的四种测量方法。对比分析各方法的测量原理、测量特点、测量效率等如下。
3.1 切片分析法
切片分析法是一种常规的检查PCB内部结构或缺陷的合规性判断方法。采用切片分析法检测PCB埋嵌铜块共面度,需要将埋嵌铜块连同周边一定尺寸的PCB切割下来制成样片,经过垂直研磨、抛光和后处理后,在金相显微镜一定倍率下(常为200X)检查埋嵌铜块相对其周边PCB基体的高度差(图5)。

显然,切片分析法检测PCB埋嵌铜块共面度是一种破坏性的检测方法,其检测耗时较长,所能检查的点有限,但其测量结果直观(可拍摄图片、在图片上量取共面度)、测量精度较高(常用200倍放大倍率下:误差为5%)。
3.2 三维坐标测量法
公司三维坐标仪原理是利用镜头的聚焦功能,记录被测样品表面被聚焦时所处的坐标(包含X、Y、Z轴坐标)。计算各测量点的Z轴坐标之差,则可得到被测样品表面的共面度值。结合埋嵌式产品特点以及公司现有设备能力现状,开发了一种埋嵌铜块共面度的测量方法,具体测量位置要求如图6所示。
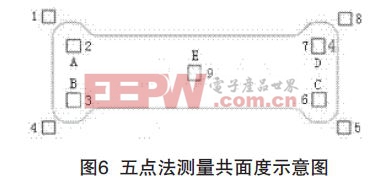
该方法使用公司三维坐标仪测量被测点的X、Y、Z坐标,所需要的测量点一般为9个,且样品表面检查点(点2、3、6、7、9)分布在被测样品(铜块)的四角和中央,具有代表性。参考点(点1、4、5、8)为被测样品四
- 专用于便携设备电源管理的超小型降压转换器(06-29)
- 级联低压差稳压器SMPS(07-12)
- 基于DSP的单相精密电源硬件设计(07-24)
- WiFi 收发器的电源和接地设计(08-12)
- 微安级数控恒流源的设计(08-20)
- 新一代手机电源管理的最佳化挑战(08-30)