电源封装趋势——元件集成方面的进步
时间:01-08
来源:互联网
点击:
作者:Ericsson营销和通信总监 Patrick Le Fevre
用户要求提高每块板的功率,在PCB上实现比以往更多的硅片,结果是高端服务器设计中日益提高的处理密度对未来电源系统产生持续影响。ICT数据服务器中每块板的功率要求已经从20世纪80年代早期的300W增加到今天的1kW以上,并且业界预测到2020年每块板将要求达到35kW的功率。目前的DC/DC电源转换器解决方案和技术还不足以达到这些功率等级。
今天,采用四分之一砖型封装的1kW DC/DC转换器已经成为现实,其功率密度指标在几年前是无法想象的。在不远的将来可以采用更先进的封装和更高集成度的元件实现八分之一砖型的1kW转换器吗?
本文将讨论电源行业在元件集成度、热管理和与当前最先进技术相比超过双倍DC/DC电源转换器密度方面会有怎样的发展趋势。
3D封装
目前的DC/DC电源转换器的砖型封装仍然是由平面两维PCB结构所主导,但要求更小封装、更低高度器件和更小寄生阻抗的客户应用正在推动技术向高密度3D封装发展。
在这些大功率砖型封装中3D封装技术的使用是受限制的,但在嵌入有源和无源器件方面很有发展前途,而PCB供应商将这个看作是向价值链上游转移的重要机会,其中包括芯片堆叠、封装堆叠以及通过二次成型实现元件嵌入。在这个领域中很重要的一点就是集成磁性材料,终极解决方案是在半导体晶圆上集成磁性元件。
在3D封装中,最常见的技术是在PCB中嵌入(有源和无源)元件。在PCB结构中嵌入元件可以帮助电源设计师显著减小外形尺寸,增强冷却能力,比如将驱动器放在靠近开关器件的位置。这种方法通过小型化和精密控制高频开关电路设计中的互连寄生阻抗可以加快提高性能和效率。今后更多元件的3D组装将进一步减小要求的外形尺寸,同时还能减小磁性元件的尺寸。
嵌入式元件可以给电源设计师提供明显的优势。然而,来自硅片行业的支持至关重要,符合标准化要求和认证测试的有源和无源器件供应链也是必需的。在合适的基础设施条件下,嵌入式技术将是提高大功率应用中功率密度的重要因素。由欧盟资助的Hermes计划已经成功地展示,大批量电源转换器的尺寸减小40%是可行的。磁隔离加上嵌入技术有望提供增强型隔离功能。通过集成控制的反馈路径也可能变成磁性路径,从而可能实现芯片级隔离型DC/DC电源转换器解决方案。
元件
大功率DC/DC转换器的开关频率通常已经针对500kHz左右或以下的工作频率进行了优化。为了方便减小尺寸,提高功率密度,将开关频率提高至2MHz及以上是有必要的,以便最大限度地减小磁体物理体积。最近刚刚商用的宽带隙(WBG)半导体器件,可以在超过5MHz的较高频率点理想地工作,比如氮化镓和砷化镓开关场效应管,已经成为更高开关频率的促进器。新的DC/DC转换器拓扑甚至会将开关频率提升到10MHz范围。这将进一步推动对采用更小寄生元件的封装要求,而这个要求完全可以利用3D集成技术实现。
PCB中嵌入式元件的商用化有助于减小发挥更高频率WBG器件优势所需的寄生阻抗,并有助于显著改善大功率DC/DC转换器的外形尺寸和效率。然而,更高开关速度依赖于低损耗高频磁性材料创新的实现,这些创新将推动商用大功率变压器和电感解决方案用于大批量生产。
实现更高频率的集成式磁性元件有多种可行的技术,包括先进的磁芯设计和磁芯材料,以及空气磁芯设计,它们能显著提高效率和功率密度。磁体的微型化有多种实用的方法,包括不依赖于磁芯材料特性的空气磁芯设计,它们也提供了生产方法方面的灵活性,以及使用不同3D集成技术的可能性,比如采用多层PCB中的嵌入式绕组以及带集成式有源铜层的多层铁氧体基板(见图1)。
图1:采用多层PCB中的嵌入式绕组以及带集成式有源铜层的多层铁氧体基板。
目前这些新技术仅限于较低功率的转换器,但通过改进磁性材料的工艺可进一步改进磁芯材料,并推广至具有较大输出电流的产品。即使在半导体晶圆中嵌入磁体实现3D集成的最终目标以及完整的单片系统集成在未来也是完全可能的。
热管理
元件和封装技术的不断发展使得额定功率越来越高,以至于现在每立方厘米瓦数的功率密度比15年前用的老技术高出了一个数量级。市场上最新的砖型电源,比如爱立信的高功率密度864W四分之一砖型电源模块,可提供37 W/cm3(600 W/in3),这对高效的内部热管理提出了很高的要求。
因为半导体器件等电子元件对高温很敏感,所以确保高功率密度砖型电源模块中的元件能被正确冷却,并以合理的温度工作很重要。除非热量传导机制特别高效,否则电源系统设计和可靠性会受到损害。
可以用于冷却电子设备的主要冷却机制是传导和对流。每个关键元件的元件功耗(Pd,comp)和元件结点到外壳热阻(Rth, J-C)变得特别重要,因为它们决定了实际的结温,而实际结温将限制DC/DC转换器的热性能,也就是在最大输出功率条件下允许的最大壳温。
元件结点(或内核)和外壳之间的温差可以用下面这个公式计算:
因此,旨在倍增功率密度(75 W/cm3 或1200 W/in3) 的先进冷却技术和用于改善新兴3D封装组件热性能的技术至关重要,它们将最终决定更高功率密度的可行性,而与任何改进的元件技术无关。
许多标准元件不适合高密度或3D设计,因此它们没有足够的热性能。在从DC/DC转换器组件提供特别高功率时要满足的其它热设计挑战包括大电流分配、连接器技术、在45层板上的组装,以及即使显著增强的传统冷却技术也显不足,比如现有的空气对流。
二次成型很可能继续成为用于提高热性能的技术,但同时也很明显,用于包括磁性元件和电容在内的所有功率元件的热增强型封装将是大势所趋,这种封装允许从至少两个对立面进行冷却,同时要求使用改进的热材料、工艺和冷却技术。下面给出了这种3D封装的一个例子。
功率元件不再是用裸片连接或热界面材料安装在PCB上,而是安装在临时载体上,周围通过电铸方式安装散热器。各种尺寸和厚度的元件可以集成在被称为集成式热阵列板(ITAP)的相同电路板上。当载体拿走时,元件的底面和顶面是共面的,非常方便明确的和优化了的热连接。与采用环氧树脂或焊接连接的传统封装元件相比,这种方法可以实现50%的热阻改善,对固定结温来说也就是说功耗可以高50%。
在联合采用液体冷却技术的堆叠芯片解决方案中,硅通孔也是一种潜在的解决方案。这里的实验结果也表明热性能可以提高50%。使用直接绑定铜(DBC)技术的组件烧结代替焊接和热油脂是另外一种可以显著提高热性能的技术。
其它潜在的冷却技术包括针对某些大功率元件的液体传导冷却和针对中小功耗元件的强制空气对流冷却。使用被动液体冷却技术(如热管道)解决局部热点的方法可能变得更加普及。热扩散加上对流空气冷却可以延长器件寿命,因为通过改进的芯片连接技术可以减小元件封装中的热阻,但对于高功率密度的直流直流转换器中要求最严格的大功耗元件来说,可能要求主动液体冷却技术(如泵和双相沸腾)。
用户要求提高每块板的功率,在PCB上实现比以往更多的硅片,结果是高端服务器设计中日益提高的处理密度对未来电源系统产生持续影响。ICT数据服务器中每块板的功率要求已经从20世纪80年代早期的300W增加到今天的1kW以上,并且业界预测到2020年每块板将要求达到35kW的功率。目前的DC/DC电源转换器解决方案和技术还不足以达到这些功率等级。
今天,采用四分之一砖型封装的1kW DC/DC转换器已经成为现实,其功率密度指标在几年前是无法想象的。在不远的将来可以采用更先进的封装和更高集成度的元件实现八分之一砖型的1kW转换器吗?
本文将讨论电源行业在元件集成度、热管理和与当前最先进技术相比超过双倍DC/DC电源转换器密度方面会有怎样的发展趋势。
3D封装
目前的DC/DC电源转换器的砖型封装仍然是由平面两维PCB结构所主导,但要求更小封装、更低高度器件和更小寄生阻抗的客户应用正在推动技术向高密度3D封装发展。
在这些大功率砖型封装中3D封装技术的使用是受限制的,但在嵌入有源和无源器件方面很有发展前途,而PCB供应商将这个看作是向价值链上游转移的重要机会,其中包括芯片堆叠、封装堆叠以及通过二次成型实现元件嵌入。在这个领域中很重要的一点就是集成磁性材料,终极解决方案是在半导体晶圆上集成磁性元件。
在3D封装中,最常见的技术是在PCB中嵌入(有源和无源)元件。在PCB结构中嵌入元件可以帮助电源设计师显著减小外形尺寸,增强冷却能力,比如将驱动器放在靠近开关器件的位置。这种方法通过小型化和精密控制高频开关电路设计中的互连寄生阻抗可以加快提高性能和效率。今后更多元件的3D组装将进一步减小要求的外形尺寸,同时还能减小磁性元件的尺寸。
嵌入式元件可以给电源设计师提供明显的优势。然而,来自硅片行业的支持至关重要,符合标准化要求和认证测试的有源和无源器件供应链也是必需的。在合适的基础设施条件下,嵌入式技术将是提高大功率应用中功率密度的重要因素。由欧盟资助的Hermes计划已经成功地展示,大批量电源转换器的尺寸减小40%是可行的。磁隔离加上嵌入技术有望提供增强型隔离功能。通过集成控制的反馈路径也可能变成磁性路径,从而可能实现芯片级隔离型DC/DC电源转换器解决方案。
元件
大功率DC/DC转换器的开关频率通常已经针对500kHz左右或以下的工作频率进行了优化。为了方便减小尺寸,提高功率密度,将开关频率提高至2MHz及以上是有必要的,以便最大限度地减小磁体物理体积。最近刚刚商用的宽带隙(WBG)半导体器件,可以在超过5MHz的较高频率点理想地工作,比如氮化镓和砷化镓开关场效应管,已经成为更高开关频率的促进器。新的DC/DC转换器拓扑甚至会将开关频率提升到10MHz范围。这将进一步推动对采用更小寄生元件的封装要求,而这个要求完全可以利用3D集成技术实现。
PCB中嵌入式元件的商用化有助于减小发挥更高频率WBG器件优势所需的寄生阻抗,并有助于显著改善大功率DC/DC转换器的外形尺寸和效率。然而,更高开关速度依赖于低损耗高频磁性材料创新的实现,这些创新将推动商用大功率变压器和电感解决方案用于大批量生产。
实现更高频率的集成式磁性元件有多种可行的技术,包括先进的磁芯设计和磁芯材料,以及空气磁芯设计,它们能显著提高效率和功率密度。磁体的微型化有多种实用的方法,包括不依赖于磁芯材料特性的空气磁芯设计,它们也提供了生产方法方面的灵活性,以及使用不同3D集成技术的可能性,比如采用多层PCB中的嵌入式绕组以及带集成式有源铜层的多层铁氧体基板(见图1)。
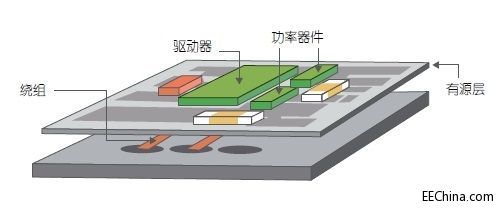
图1:采用多层PCB中的嵌入式绕组以及带集成式有源铜层的多层铁氧体基板。
目前这些新技术仅限于较低功率的转换器,但通过改进磁性材料的工艺可进一步改进磁芯材料,并推广至具有较大输出电流的产品。即使在半导体晶圆中嵌入磁体实现3D集成的最终目标以及完整的单片系统集成在未来也是完全可能的。
热管理
元件和封装技术的不断发展使得额定功率越来越高,以至于现在每立方厘米瓦数的功率密度比15年前用的老技术高出了一个数量级。市场上最新的砖型电源,比如爱立信的高功率密度864W四分之一砖型电源模块,可提供37 W/cm3(600 W/in3),这对高效的内部热管理提出了很高的要求。
因为半导体器件等电子元件对高温很敏感,所以确保高功率密度砖型电源模块中的元件能被正确冷却,并以合理的温度工作很重要。除非热量传导机制特别高效,否则电源系统设计和可靠性会受到损害。
可以用于冷却电子设备的主要冷却机制是传导和对流。每个关键元件的元件功耗(Pd,comp)和元件结点到外壳热阻(Rth, J-C)变得特别重要,因为它们决定了实际的结温,而实际结温将限制DC/DC转换器的热性能,也就是在最大输出功率条件下允许的最大壳温。
元件结点(或内核)和外壳之间的温差可以用下面这个公式计算:

因此,旨在倍增功率密度(75 W/cm3 或1200 W/in3) 的先进冷却技术和用于改善新兴3D封装组件热性能的技术至关重要,它们将最终决定更高功率密度的可行性,而与任何改进的元件技术无关。
许多标准元件不适合高密度或3D设计,因此它们没有足够的热性能。在从DC/DC转换器组件提供特别高功率时要满足的其它热设计挑战包括大电流分配、连接器技术、在45层板上的组装,以及即使显著增强的传统冷却技术也显不足,比如现有的空气对流。
二次成型很可能继续成为用于提高热性能的技术,但同时也很明显,用于包括磁性元件和电容在内的所有功率元件的热增强型封装将是大势所趋,这种封装允许从至少两个对立面进行冷却,同时要求使用改进的热材料、工艺和冷却技术。下面给出了这种3D封装的一个例子。
功率元件不再是用裸片连接或热界面材料安装在PCB上,而是安装在临时载体上,周围通过电铸方式安装散热器。各种尺寸和厚度的元件可以集成在被称为集成式热阵列板(ITAP)的相同电路板上。当载体拿走时,元件的底面和顶面是共面的,非常方便明确的和优化了的热连接。与采用环氧树脂或焊接连接的传统封装元件相比,这种方法可以实现50%的热阻改善,对固定结温来说也就是说功耗可以高50%。
在联合采用液体冷却技术的堆叠芯片解决方案中,硅通孔也是一种潜在的解决方案。这里的实验结果也表明热性能可以提高50%。使用直接绑定铜(DBC)技术的组件烧结代替焊接和热油脂是另外一种可以显著提高热性能的技术。
其它潜在的冷却技术包括针对某些大功率元件的液体传导冷却和针对中小功耗元件的强制空气对流冷却。使用被动液体冷却技术(如热管道)解决局部热点的方法可能变得更加普及。热扩散加上对流空气冷却可以延长器件寿命,因为通过改进的芯片连接技术可以减小元件封装中的热阻,但对于高功率密度的直流直流转换器中要求最严格的大功耗元件来说,可能要求主动液体冷却技术(如泵和双相沸腾)。
PCB 半导体 电路 嵌入式 场效应管 变压器 电感 电流 电源模块 电子 连接器 电容 相关文章:
- 适合高效能模拟应用的线性电压稳压器(07-19)
- 构建一个低成本的9V电池电压监控器(07-28)
- 主动“ORing”方案降低了功率损耗和设备尺寸(06-24)
- 开关电源要降低纹波主要要在三个方面下功夫(06-24)
- TI以独特的芯片结构和散热封装叩关功率MOSFET市场(01-26)
- DC/DC电源管理应用中的功率MOSFET的热分析方法(12-10)