可用于生产线的工业机器人研究
时间:11-04
来源:互联网
点击:
1简介
随着信息技术、材料技术、新能源技术等新技术与制造技术的相互交叉、渗透、融合,现在的制造业与过去相比有了许多重大而深刻的变化。El益增长的复杂性是现在制造业的一个重要特点,这不仅表现在制造系统中,还表现在所制造的产品,制造过程以及企业的结构中。这种复杂性为工业机器人的发展提供了一个好的机遇,当然,也是一种挑战!东莞理工学院处于东莞松山湖高新开发区,东莞作为一个现代制造业名城,正处于产业转型的最关键时期,如果能适时的把工业机器人应用到各企业生产线的改造中,无疑将有着巨大的空间和前景。
本工业机器人是一种精密型装配机器人,采用四轴伺服电机驱动控制,实现四轴空间联动,配置不同工具包可实现搬运、码垛、装配等工作,具有速度快、精度高、柔性好等特点,采用交流伺机服电机驱动,由操作机(机械本体)、控制器、伺服驱动系统和传感装置构成:
(1)操作机:通过有限元分析、模态分析及仿真设计等现代设计方法的运用,机器人操作机已实现了优化设计。
(2)控制器:由开始应用香港固高科技有限公司的GT系列运动控制器到自主开发基于ARM9的控制器,并且实现了软件伺服和全数字控制。
(3)伺服驱动系统:采用富士伺服器。
(4)传感装置:正在尝试使用激光传感器、视觉传感器和力传感器在机器人系统中应用,这样就能实现自动化生产线上物体的自动定位以及精密装配作业等,大大提高了机器人的作业性能和对环境的适应性。
(5)网络通信:机器人控制器已实现了与Canbus、Profibus总线及一些网络的连接,使机器人由过去的独立应用向网络化应用迈进了一大步,也使机器人由过去的专用设备向标准化设备发展。
2数据通信方式
由于串行通信所用的传输线少,传输的距离长,有利于实时控制和管理,所以本系统采用了串行通信方式,“串行通信”时,数据在一根数据线上~位一位地进行传输,每一位数据都占用某一固定的时间段,但由于计算机CPU与接口之间按并行方式传输,接口与外设之间按串行方式传输,因此在串行接口中必须有“接受移位寄存器”和“发送移位寄存器”,负责串行数据和并行数据间的转换,能够完成“串——>并”转换功能的电路称为“通用异步收发器”。在传输的速度上,串行通信明显低于并口通信,但是串行通信的成本低、通信距离长的优势是显而易见的。
信息传输在一个方向上只占用一根通信线,这根线既作数据线又作联络线,上位机与机器人间的协议按照如下三个级别来组织的。
(1)物理层:是指用来执行这种通信的硬件,包括数据线和控制线本系统中采用RS232串口,机器人一端为9针D形接头,另一端RJ-45接头连到了终端服务器TerminalServer扩展的串行接口上,然后通过终端服务器的网络接口与FMS局域网相连、最终实现与机器人控制算机的连接。硬件平台如图1。
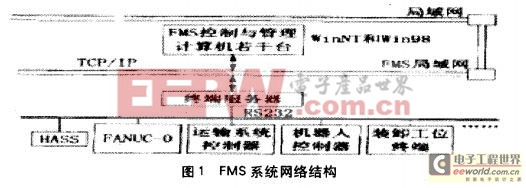
(2)数据链路层:该层是一种低级的通信协议,该协议利用发送与接受特殊的控制字符确保信息可靠的发送。工业机器人控制器与上位计算机之间的信息交换由字符串组成,该字符串包括实际要交换的信息以及附加的控制字符,附加字符是必须的,以便接受设备能够决定是否已接受到一个完整的信息。发送一个机器人的控制指令,需要经过以下六个阶段:发送开相、打包发送、发送闭相、接受开相、接受解包和接受闭相。
(3)应用层:该层是一种高级的通信协议,该协议定义了每一种信息的内容以及每一种信息的响应。机器人控制器接受到一个信息后,信息必须由其控制器负责译码,并作出相应的动作,能够响应上位计算机信息指令的软件就称为应用级协议。在本系统中,主要由上位机发送L0ADV、SAVEV、JwAIT、START四类指令,实现微机启动机器人并进行实时监控。
3控制器
如何有效地将其他领域(如图像处理、声音识别、最优控制、人工智能等)的研究成果应用到机器人控制系统的实时操作中,是一项富有挑战性的研究工作.而具有开放式结构的模块化、标准化机器人控制器的研究无疑对提高机器人性能和自主能力、推动机器人技术的发展具有重大意义.机器人控制器是根据指令以及传感信息控制机器人完成一定的动作或作业任务的装置,它是机器人的心脏,决定了机器人性能的优劣。
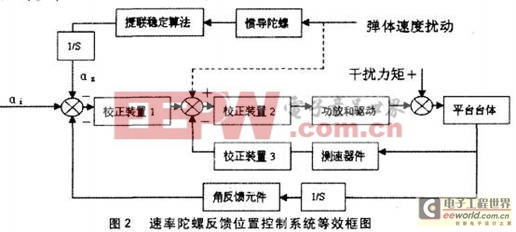
这里采用了串行的控制算法处理方式,机器人的控制算法是由串行机来处理。用上、下位机二级分布式结构,上位机负责整个系统管理以及运动学计算、轨迹规划等。下位机由多CPU组成,每个CPU控制一个关节运动,这些CPU和主控机联系是通过总线形式的紧耦合。这种结构的控制器工作速度和控制性能明显提高,但这些多CPU系统共有的特征都是针对具体问题而采用的功能分布式结构,即每个处理器承担固定任务,控制器计算机控制系统中的位置控制部分,采用数字式位置控制。硬件平台本一开始采用固高公司生产的GT系列运动控制器,可以同步控制四个运动轴,实现多轴协调运动。其核心由ADSP2I8l数字信号处理器和FPGA组成,可以实现高性能的控制计算。研究过程中,有以下几个局限性:
(1)开放性差:局限于“专用计算机、专用机器人语言、专用微处理器”的封闭式结构。封闭的控制器结构使其具有特定的功能、适应于特定的环境,不便于对系统进行扩展和改进;
(2)软件独立性差:软件结构及其逻辑结构依赖于处理器硬件,难以在不同的系统间移植;
(3)容错性差:由于并行计算中的数据相关性、通讯及同步等内在特点,控制器的容错性能变差,其中一个处理器出故障可能导致整个系统的瘫痪;
(4)扩展性差:目前,机器人控制器的研究着重于从关节这一级较常见的,比如对空宅导弹导引火来说,锁定和预偏是两个经常要用到的功能,而它们却对伺服系统的形式和速率传感器的选择提出丁不同的要求。
首先,如果在导引头内增加一套测速机元什,则问题就可以解决,但这样做会使系统复杂程度提高,利于产品研制的工程化和小型化;再者,通过计算分析发现,在导弹的挂帆飞行状态,导引光轴虽然要求复现的是相对弹体的锁定,搜索和雷达黼动信号,但导弹住挂机状态弹体摆动角速度不是太大,且摆动持续的时间也不会很长,如果导引头的锁定品质能满足要求,则利用速率陀螺来进行反馈的弊端就可被大大减弱。所以经过综合考虑,决定仍仅采用速率陀螺作为内回路速度传感器件,以科于更好地实现光轴对El标的稳定跟踪。
4仿真验证
以随动系统复现相对惯性空间稳定的输入为例,为进一步比较两种方案,我们利用ADAMs软件和MATLAB软件一起进行了位标器运动学、动『J学和控制系统联合仿真。仿真条件假设目标在空间静止,在中环通道,分别利用陀螺速度反馈和测速机速度反馈,在弹体摆动情况下,进行目标指示信息的随动,对指向误差(即光轴与视线的夹角)的大小进行记录,仿真结果如图3所示。
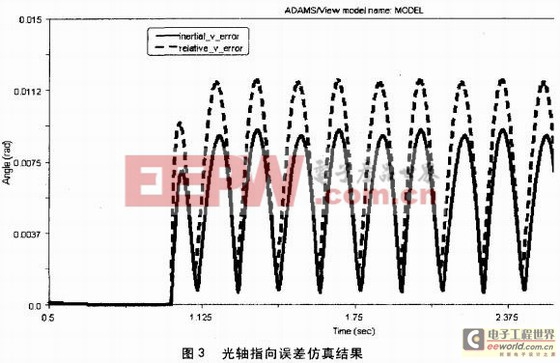
其中实线为采用陀螺信号时的误差,虚线为采用测速机信号时的误差。结果表明,采用陀螺信号作为反馈信号可以有效地减小弹体摆动情况系统的随动误差,此结果与前面理论分析结果也基本一致。
5结语
本文详细分析了动基座随动系统不同输入信号的类型,得出对相对基座稳定的输入采用测速机反馈、对相对惯性空间稳定的输入采用速率陀螺反馈的传感器选用原则,并以空空导弹导引头为例进行了ADAMs和MATLAB联合数字仿真,仿真结果验证了分析的正确性。
参考文献:
左哲,李东海,戴亚平,宋跃进.陀螺稳定平台状态补偿控制.航空学报,2008,29(1):14l47.
杨蒲,李奇.三轴陀螺稳定平台控制系统设计与实现.中国惯性技术学报,2007,15(2):176.
随着信息技术、材料技术、新能源技术等新技术与制造技术的相互交叉、渗透、融合,现在的制造业与过去相比有了许多重大而深刻的变化。El益增长的复杂性是现在制造业的一个重要特点,这不仅表现在制造系统中,还表现在所制造的产品,制造过程以及企业的结构中。这种复杂性为工业机器人的发展提供了一个好的机遇,当然,也是一种挑战!东莞理工学院处于东莞松山湖高新开发区,东莞作为一个现代制造业名城,正处于产业转型的最关键时期,如果能适时的把工业机器人应用到各企业生产线的改造中,无疑将有着巨大的空间和前景。
本工业机器人是一种精密型装配机器人,采用四轴伺服电机驱动控制,实现四轴空间联动,配置不同工具包可实现搬运、码垛、装配等工作,具有速度快、精度高、柔性好等特点,采用交流伺机服电机驱动,由操作机(机械本体)、控制器、伺服驱动系统和传感装置构成:
(1)操作机:通过有限元分析、模态分析及仿真设计等现代设计方法的运用,机器人操作机已实现了优化设计。
(2)控制器:由开始应用香港固高科技有限公司的GT系列运动控制器到自主开发基于ARM9的控制器,并且实现了软件伺服和全数字控制。
(3)伺服驱动系统:采用富士伺服器。
(4)传感装置:正在尝试使用激光传感器、视觉传感器和力传感器在机器人系统中应用,这样就能实现自动化生产线上物体的自动定位以及精密装配作业等,大大提高了机器人的作业性能和对环境的适应性。
(5)网络通信:机器人控制器已实现了与Canbus、Profibus总线及一些网络的连接,使机器人由过去的独立应用向网络化应用迈进了一大步,也使机器人由过去的专用设备向标准化设备发展。
2数据通信方式
由于串行通信所用的传输线少,传输的距离长,有利于实时控制和管理,所以本系统采用了串行通信方式,“串行通信”时,数据在一根数据线上~位一位地进行传输,每一位数据都占用某一固定的时间段,但由于计算机CPU与接口之间按并行方式传输,接口与外设之间按串行方式传输,因此在串行接口中必须有“接受移位寄存器”和“发送移位寄存器”,负责串行数据和并行数据间的转换,能够完成“串——>并”转换功能的电路称为“通用异步收发器”。在传输的速度上,串行通信明显低于并口通信,但是串行通信的成本低、通信距离长的优势是显而易见的。
信息传输在一个方向上只占用一根通信线,这根线既作数据线又作联络线,上位机与机器人间的协议按照如下三个级别来组织的。
(1)物理层:是指用来执行这种通信的硬件,包括数据线和控制线本系统中采用RS232串口,机器人一端为9针D形接头,另一端RJ-45接头连到了终端服务器TerminalServer扩展的串行接口上,然后通过终端服务器的网络接口与FMS局域网相连、最终实现与机器人控制算机的连接。硬件平台如图1。
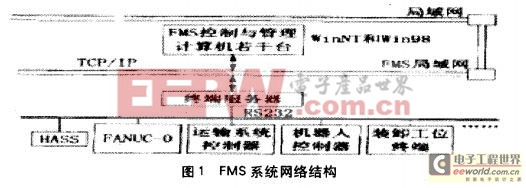
(2)数据链路层:该层是一种低级的通信协议,该协议利用发送与接受特殊的控制字符确保信息可靠的发送。工业机器人控制器与上位计算机之间的信息交换由字符串组成,该字符串包括实际要交换的信息以及附加的控制字符,附加字符是必须的,以便接受设备能够决定是否已接受到一个完整的信息。发送一个机器人的控制指令,需要经过以下六个阶段:发送开相、打包发送、发送闭相、接受开相、接受解包和接受闭相。
(3)应用层:该层是一种高级的通信协议,该协议定义了每一种信息的内容以及每一种信息的响应。机器人控制器接受到一个信息后,信息必须由其控制器负责译码,并作出相应的动作,能够响应上位计算机信息指令的软件就称为应用级协议。在本系统中,主要由上位机发送L0ADV、SAVEV、JwAIT、START四类指令,实现微机启动机器人并进行实时监控。
3控制器
如何有效地将其他领域(如图像处理、声音识别、最优控制、人工智能等)的研究成果应用到机器人控制系统的实时操作中,是一项富有挑战性的研究工作.而具有开放式结构的模块化、标准化机器人控制器的研究无疑对提高机器人性能和自主能力、推动机器人技术的发展具有重大意义.机器人控制器是根据指令以及传感信息控制机器人完成一定的动作或作业任务的装置,它是机器人的心脏,决定了机器人性能的优劣。
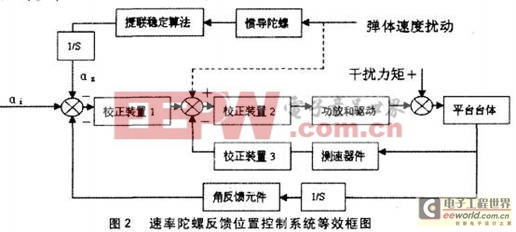
这里采用了串行的控制算法处理方式,机器人的控制算法是由串行机来处理。用上、下位机二级分布式结构,上位机负责整个系统管理以及运动学计算、轨迹规划等。下位机由多CPU组成,每个CPU控制一个关节运动,这些CPU和主控机联系是通过总线形式的紧耦合。这种结构的控制器工作速度和控制性能明显提高,但这些多CPU系统共有的特征都是针对具体问题而采用的功能分布式结构,即每个处理器承担固定任务,控制器计算机控制系统中的位置控制部分,采用数字式位置控制。硬件平台本一开始采用固高公司生产的GT系列运动控制器,可以同步控制四个运动轴,实现多轴协调运动。其核心由ADSP2I8l数字信号处理器和FPGA组成,可以实现高性能的控制计算。研究过程中,有以下几个局限性:
(1)开放性差:局限于“专用计算机、专用机器人语言、专用微处理器”的封闭式结构。封闭的控制器结构使其具有特定的功能、适应于特定的环境,不便于对系统进行扩展和改进;
(2)软件独立性差:软件结构及其逻辑结构依赖于处理器硬件,难以在不同的系统间移植;
(3)容错性差:由于并行计算中的数据相关性、通讯及同步等内在特点,控制器的容错性能变差,其中一个处理器出故障可能导致整个系统的瘫痪;
(4)扩展性差:目前,机器人控制器的研究着重于从关节这一级较常见的,比如对空宅导弹导引火来说,锁定和预偏是两个经常要用到的功能,而它们却对伺服系统的形式和速率传感器的选择提出丁不同的要求。
首先,如果在导引头内增加一套测速机元什,则问题就可以解决,但这样做会使系统复杂程度提高,利于产品研制的工程化和小型化;再者,通过计算分析发现,在导弹的挂帆飞行状态,导引光轴虽然要求复现的是相对弹体的锁定,搜索和雷达黼动信号,但导弹住挂机状态弹体摆动角速度不是太大,且摆动持续的时间也不会很长,如果导引头的锁定品质能满足要求,则利用速率陀螺来进行反馈的弊端就可被大大减弱。所以经过综合考虑,决定仍仅采用速率陀螺作为内回路速度传感器件,以科于更好地实现光轴对El标的稳定跟踪。
4仿真验证
以随动系统复现相对惯性空间稳定的输入为例,为进一步比较两种方案,我们利用ADAMs软件和MATLAB软件一起进行了位标器运动学、动『J学和控制系统联合仿真。仿真条件假设目标在空间静止,在中环通道,分别利用陀螺速度反馈和测速机速度反馈,在弹体摆动情况下,进行目标指示信息的随动,对指向误差(即光轴与视线的夹角)的大小进行记录,仿真结果如图3所示。
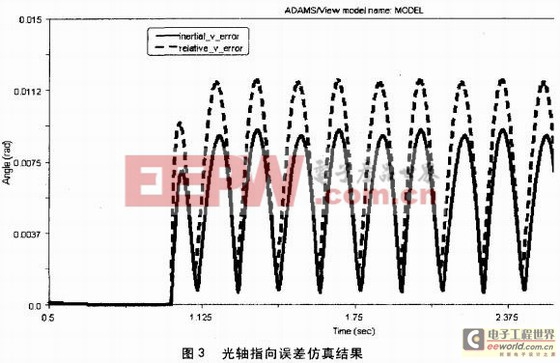
其中实线为采用陀螺信号时的误差,虚线为采用测速机信号时的误差。结果表明,采用陀螺信号作为反馈信号可以有效地减小弹体摆动情况系统的随动误差,此结果与前面理论分析结果也基本一致。
5结语
本文详细分析了动基座随动系统不同输入信号的类型,得出对相对基座稳定的输入采用测速机反馈、对相对惯性空间稳定的输入采用速率陀螺反馈的传感器选用原则,并以空空导弹导引头为例进行了ADAMs和MATLAB联合数字仿真,仿真结果验证了分析的正确性。
参考文献:
左哲,李东海,戴亚平,宋跃进.陀螺稳定平台状态补偿控制.航空学报,2008,29(1):14l47.
杨蒲,李奇.三轴陀螺稳定平台控制系统设计与实现.中国惯性技术学报,2007,15(2):176.
- 可编程机器人将替代码农 可改装来自工业机器人(06-04)
- 贴砖工程自动化 建筑机器人可提高4倍生产效率(12-20)
- 工业机器人在中国:由低端开始,向高端进发(12-20)
- 伺服在工业机器人技术中的运用(12-19)
- 实现高效生产的工业机器人(12-20)
- 工业机器人在缝纫机铸件加工中的应用(12-20)