数字隔离器在工业电机驱动应用中的优势
时间:12-16
来源:互联网
点击:
简介
工业电机驱动中使用的电子控制必须能在恶劣的电气环境中提供较高的系统性能。电源电路会在电机绕组上导致电压沿激增现象,而这些电压沿则可以电容耦合进低电压电路之中。电源电路中,电源开关和寄生元件的非理想行为也会产生感性耦合噪声。控制电路与电机和传感器之间的长电缆形成多种路径,可将噪声耦合到控制反馈信号中。高性能驱动器需要必须与高噪声电源电路隔离开的高保真反馈控制和信号。在典型的驱动系统中,包括隔离栅极驱动信号,以便将逆变器、电流和位置反馈信号驱动到电机控制器,以及隔离各子系统之间的通信信号。实现信号隔离时,不得牺牲信号路径的带宽,也不得显著增加系统成本。光耦合器是跨越隔离栅实现安全隔离的传统方法。尽管光耦合器已使用数十年,其不足也会影响系统级性能。
变速电机驱动器在工业应用中的广泛使用要归功于高效电源开关和具有成本优势的电子控制电路。设计上的困难则是用低压控制电路耦合高功率开关电路,而不牺牲抗噪性能或开关速度。
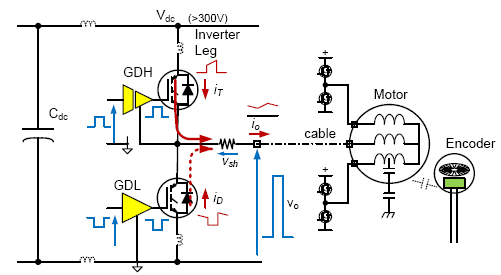
图1. 包括寄生元件的逆变器电路。
现代开关逆变器的效率一般超过95%,所用功率晶体管开关还可连接高压直流轨高轨与低轨之间的电机绕组。这一过程可以减少逆变器的损耗,因为功率晶体管工作于完全饱和模式下,而该模式会降低传导时的压降和功率损耗。开关过程中还存在额外的功率晶体管损耗,因为在此期间,晶体管上有一较大的电压,与此同时,负载电流在高、低功率设备之间进行切换。功率半导体公司设计出IGBT之类开关时间较短的晶体管,以减少这种开关功率损耗。然而,这种较高的开关速度也会带来一些无用的副作用,比如开关噪声增加。
在驱动器控制端,VLSI工艺的持续进步改善了混合信号控制电路的成本和性能,为高级数字控制算法的广泛应用以及交流电机效率的提高创造了条件。提升性能付出的代价是IC工作电压从12 V至5 V降低至现在的3.3 V,结果提高了对噪声的灵敏度。这种传统的噪声过滤方法通常不太适用,因为往往需要维持驱动系统的带宽,而带宽一般都是一个关键的性能参数。
电机驱动逆变器环境
三相逆变器是一种功率电子开关电路,控制功率从直流供电轨到三个交流电机绕组的流动。逆变器有三条相同的腿,每条腿包括两个IGBT晶体管和两个二极管,如图1所示。每个电机绕组均连接至通过分流器连接高端晶体管和低端晶体管的同一节点。逆变器使电机绕组在直流总线的高压轨和低压轨之间切换,以控制平均电压。绕组具有极高的电感性,将阻挡电流的变化,因此,当功率晶体管关闭时,电流将开始在连接至相反电源轨的二极管中流动。这样,即使逆变器功率设备和直流链路电容中存在断续传导,也会有电流连续流到电机绕组中。电机绕组阻抗充当来自逆变器的高压脉冲宽度调制方波输出电压的低通滤波器。
将低压控制电流连接至逆变器时存在巨大的困难。一个基本问题是,高端晶体管发射器节点在高压总线高供电轨与低供电轨之间切换。首先,高端驱动器必须能够驱动相对于一个发射器(可能比共用输入信号高300 V或以上)的栅极信号。其次,通过分流器(vsh)的电机电流信号必须从300 V或以上的共模电压中提取出来。其他问题将由电源电路中的寄生元件导致。当功率晶体管或二极管的开关频率超过1 A/ns时,即使是10 nH的PCB走线电感也可能导致显著的电压(>10 V)。寄生电感和部件电感会导致振铃,结果使设备开关产生的噪声脉冲的持续时间变长。甚至电机电缆的高频阻抗也可能带来问题,因为出于安全考虑,配电板可能离电机很远。其他效应包括噪声从电机耦合到反馈传感器信号中,其原因是快速切换的绕组电压波形。问题将变得更加严重,因为驱动电路的功率额定值将增加电路板的物理尺寸,结果将进一步增加寄生电感,甚至提高电流和电压开关速率。通过隔离控制和电源电路消除噪声耦合现象,是应对这一问题的主要工具之一。隔离电路的性能是决定驱动性能的一个关键因素。在转轴转动时,转轴位置编码器将产生频率为100 kHz或以上的数字脉冲流。然而,在许多情况下,编码器上安装的电路会提高设备的精度,并使数据速率增加到10 Mbps以上。另外,跨越分流器的反馈信号也可以隔离,方法是先把数据转换成数字位流,然后把该位流与低功耗电路隔离开来。这种情况下,数据速率为10 Mbps至20 Mbps。
栅极驱动电路所需要的开关性能似乎并不高,因为电机驱动逆变器的开关速率很少超过20 kHz。然而,需要在高端设备和低端设备的开关信号之间插入一个死区,以防止发生直通。死区为功率开关的开启和关闭延迟以及隔离电路所致延迟的不确定性的函数。死区延长会给逆变器传递函数带来更多非线性,结果将产生无用的电流谐波,并可能降低驱动效率。
因此,跨越电源电路和控制电路之间的隔离栅发送数据的方法不得在开关过程中带来时序的不确定性,并须具备较强的抗噪能力。
隔离器技术传输速率比较
隔离不得给整体系统性能带来任何显著的时序不确定性或时序误差。标准光耦合器的传播延迟为微秒级,可能因器件而异,因温度和寿命而异。光耦合器技术在时序性能方面存在一些根本的不足,而现代数字隔离器采用完全不同的运算原则,其速率也更高。
可以在有所折衷的情况下增加光耦合器的速率。光耦合器的工作原理是,将来自LED的光发送至一种光学透明的隔离材料,并用另一端的光电二极管检测光。光耦合器的速度与光电二极管检波器的速率以及为其二极管电容充电的时间直接相关。减少传播延迟的一种方法是增加发射的光量。通过提高LED电流,可以使延迟减少2或3倍,但其代价是设备功耗会增加,每个数据通道最高将达50 mW。
提高速度的另一种办法是通过使用更薄的隔离栅来减少光传输损耗。为了维持相同的隔离能力,需要增加一层材料,但代价是成本也将增高。更快的光耦合器比标准的低成本光耦合器要贵许多倍。
相反,数字隔离器则是采用标准的高速CMOS工艺,并搭载隔离式片内微变压器。其传输速率自然比光耦合器快很多。较高的速度是电路和设计与生俱来的特点,不需要更复杂、成本更高的隔离材料也可实现更高的速度。变压器可以以最高150 Mbps的传输速率传递数据,传播延迟低至32 ns,功耗<5 mW,开关速率为25 kHz或以上。速度更快的另一个好处是,通道间的匹配优于5 ns,比标准光耦合器高出了一个数量级,仅以大约一半的单位通道成本即可实现比光耦合器快3至4倍的卓越性能。
隔离的抗噪性
在电机驱动系统中,隔离还提供了一个分离噪声源的机会,方法是以电流方式将噪声从功率开关电路和控制电路之中隔离开来。以下各项之间有安全隔离需求:高压总线、线路电压和用户界面,以同时保护人、保护其他设备。还需要在功能上使高端开关和低端开关与控制电路相隔离。隔离元件必须能提供必要的隔离,同时也需对嘈杂环境不敏感。
衡量隔离器分离地域之间高速噪声的能力的指标一般称为共模瞬变抗扰度(CMTI)。CMTI旨在衡量一个隔离器在隔离器数据通信不被噪声打断的情况下,对隔离栅中的电压噪声的抑制能力。其单位是kV/μs瞬变。
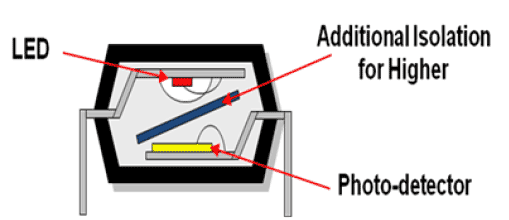
图2. 光耦合器内部结构。
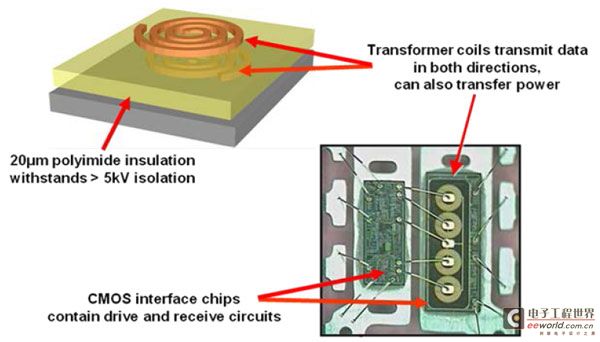
图3. 基于变压器的数字隔离器的结构。
电压瞬变噪声跨越隔离栅的路径一般是寄生电容跨过隔离器中的隔离栅。光耦合器的CMTI一般较差,为15 kV/μs。一些现代数字隔离器采用电容耦合数据隔离技术,其信号和共模噪声使用同一路径。基于变压器的隔离器(如ADI的iCoupler数字隔离器)的信号路径不同于噪声路径,其CMTI的值一般为50 kV/μs或以上。
隔离材料和可靠性
数字隔离器采用晶圆CMOS工艺制造,仅限于常用的晶圆材料。非标准材料会使生产复杂化,导致可制造性变差且成本提高。常用的绝缘材料包括聚合物(如聚酰亚胺PI,它可以旋涂成薄膜)和二氧化硅(SiO2)。二者均具有众所周知的绝缘特性,并且已经在标准半导体工艺中使用多年。聚合物是许多光耦合器的基础,作为高压绝缘体具有悠久的历史。
安全标准通常规定1分钟耐压额定值(典型值2.5 kV rms至5 kV rms)和工作电压(典型值125 V rms至400 V rms)。某些标准也会规定更短的持续时间、电压浪涌(如10 kV峰值并持续50 μs)作为增强绝缘认证的一部分要求。聚合物/聚酰亚胺隔离器可提供最好的隔离特性(见表1)。
表1. 隔离材料性能比较
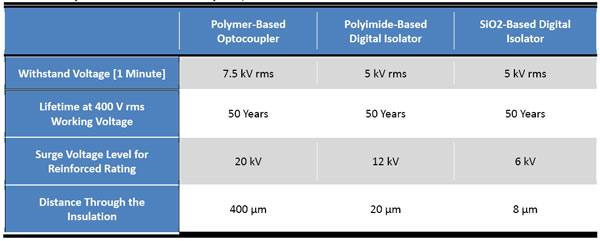
聚酰亚胺数字隔离器与光耦合器类似,在典型工作电压下,工作寿命超过电机,额定使用寿命为50年。SiO2隔离器的工作寿命与之接近,但是,对高能浪涌的保护能力却较弱。
在高温连续使用的情况下,影响光耦合器寿命的可能不是隔离材料的分解而是LED磨损。当温度>85℃时,工作1万小时,光耦合器的电流传输比(CTR)将下降10%至20%。10万小时时,CTR可能会下降一半或以上。
集成可能性
光耦合器LED和优化的光检波器不兼容低成本CMOS技术。要集成带去饱和检测功能的栅极驱动、用∑-△ADC实现隔离电流检测以及多向数据流等其他功能,就必须采用多芯片解决方案,结果将使带这些功能的光耦合器变得非常昂贵。采用CMOS技术和隔离式变压器的数字隔离器可以随着集成度的提高而自然而然地添加这些功能。由于变压器也可用来发射隔离功率,因此,可从相同的封装发射高端功率,而无需会给某些应用带来问题的自举。目前,市场上有基于变压器的数字隔离器,在单个封装中集成了dc/dc转换器、∑-△ ADC、栅极驱动器、I2C、RS-485收发器、RS-232收发器和CAN收发器,使电机控制系统同时实现了尺寸和成本的优化。
实用的应用电路
展示了栅极驱动、通信和反馈信号隔离的典型驱动电路如图4所示。在该系统中,隔离的∑-△ ADC用来测量电机绕组电流,数字位流则由电机控制IC上的数字过滤电路进行处理。位置编码器包含一个ASIC,由其通过一个隔离式RS-485接口将位置和速度数据发送给电机控制IC。其他隔离式串行接口包括连接PFC的I2C接口以及连接前面板的隔离式RS-232链路。在此例中,PWM信号与逆变器模块隔离,IGBT由一个嵌入该模块中的电平转换栅极驱动器驱动。
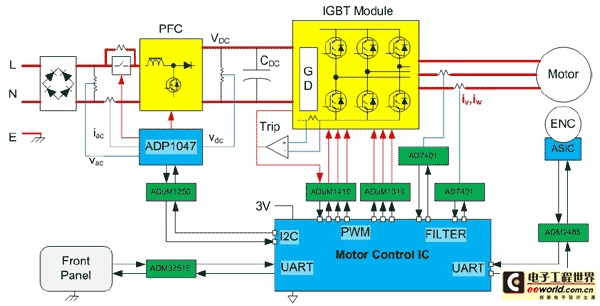
图4. 典型的中型工业电机驱动系统。
工业电机驱动中使用的电子控制必须能在恶劣的电气环境中提供较高的系统性能。电源电路会在电机绕组上导致电压沿激增现象,而这些电压沿则可以电容耦合进低电压电路之中。电源电路中,电源开关和寄生元件的非理想行为也会产生感性耦合噪声。控制电路与电机和传感器之间的长电缆形成多种路径,可将噪声耦合到控制反馈信号中。高性能驱动器需要必须与高噪声电源电路隔离开的高保真反馈控制和信号。在典型的驱动系统中,包括隔离栅极驱动信号,以便将逆变器、电流和位置反馈信号驱动到电机控制器,以及隔离各子系统之间的通信信号。实现信号隔离时,不得牺牲信号路径的带宽,也不得显著增加系统成本。光耦合器是跨越隔离栅实现安全隔离的传统方法。尽管光耦合器已使用数十年,其不足也会影响系统级性能。
变速电机驱动器在工业应用中的广泛使用要归功于高效电源开关和具有成本优势的电子控制电路。设计上的困难则是用低压控制电路耦合高功率开关电路,而不牺牲抗噪性能或开关速度。
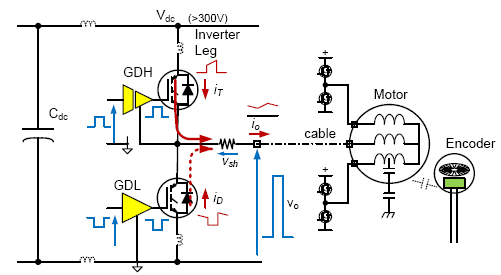
图1. 包括寄生元件的逆变器电路。
现代开关逆变器的效率一般超过95%,所用功率晶体管开关还可连接高压直流轨高轨与低轨之间的电机绕组。这一过程可以减少逆变器的损耗,因为功率晶体管工作于完全饱和模式下,而该模式会降低传导时的压降和功率损耗。开关过程中还存在额外的功率晶体管损耗,因为在此期间,晶体管上有一较大的电压,与此同时,负载电流在高、低功率设备之间进行切换。功率半导体公司设计出IGBT之类开关时间较短的晶体管,以减少这种开关功率损耗。然而,这种较高的开关速度也会带来一些无用的副作用,比如开关噪声增加。
在驱动器控制端,VLSI工艺的持续进步改善了混合信号控制电路的成本和性能,为高级数字控制算法的广泛应用以及交流电机效率的提高创造了条件。提升性能付出的代价是IC工作电压从12 V至5 V降低至现在的3.3 V,结果提高了对噪声的灵敏度。这种传统的噪声过滤方法通常不太适用,因为往往需要维持驱动系统的带宽,而带宽一般都是一个关键的性能参数。
电机驱动逆变器环境
三相逆变器是一种功率电子开关电路,控制功率从直流供电轨到三个交流电机绕组的流动。逆变器有三条相同的腿,每条腿包括两个IGBT晶体管和两个二极管,如图1所示。每个电机绕组均连接至通过分流器连接高端晶体管和低端晶体管的同一节点。逆变器使电机绕组在直流总线的高压轨和低压轨之间切换,以控制平均电压。绕组具有极高的电感性,将阻挡电流的变化,因此,当功率晶体管关闭时,电流将开始在连接至相反电源轨的二极管中流动。这样,即使逆变器功率设备和直流链路电容中存在断续传导,也会有电流连续流到电机绕组中。电机绕组阻抗充当来自逆变器的高压脉冲宽度调制方波输出电压的低通滤波器。
将低压控制电流连接至逆变器时存在巨大的困难。一个基本问题是,高端晶体管发射器节点在高压总线高供电轨与低供电轨之间切换。首先,高端驱动器必须能够驱动相对于一个发射器(可能比共用输入信号高300 V或以上)的栅极信号。其次,通过分流器(vsh)的电机电流信号必须从300 V或以上的共模电压中提取出来。其他问题将由电源电路中的寄生元件导致。当功率晶体管或二极管的开关频率超过1 A/ns时,即使是10 nH的PCB走线电感也可能导致显著的电压(>10 V)。寄生电感和部件电感会导致振铃,结果使设备开关产生的噪声脉冲的持续时间变长。甚至电机电缆的高频阻抗也可能带来问题,因为出于安全考虑,配电板可能离电机很远。其他效应包括噪声从电机耦合到反馈传感器信号中,其原因是快速切换的绕组电压波形。问题将变得更加严重,因为驱动电路的功率额定值将增加电路板的物理尺寸,结果将进一步增加寄生电感,甚至提高电流和电压开关速率。通过隔离控制和电源电路消除噪声耦合现象,是应对这一问题的主要工具之一。隔离电路的性能是决定驱动性能的一个关键因素。在转轴转动时,转轴位置编码器将产生频率为100 kHz或以上的数字脉冲流。然而,在许多情况下,编码器上安装的电路会提高设备的精度,并使数据速率增加到10 Mbps以上。另外,跨越分流器的反馈信号也可以隔离,方法是先把数据转换成数字位流,然后把该位流与低功耗电路隔离开来。这种情况下,数据速率为10 Mbps至20 Mbps。
栅极驱动电路所需要的开关性能似乎并不高,因为电机驱动逆变器的开关速率很少超过20 kHz。然而,需要在高端设备和低端设备的开关信号之间插入一个死区,以防止发生直通。死区为功率开关的开启和关闭延迟以及隔离电路所致延迟的不确定性的函数。死区延长会给逆变器传递函数带来更多非线性,结果将产生无用的电流谐波,并可能降低驱动效率。
因此,跨越电源电路和控制电路之间的隔离栅发送数据的方法不得在开关过程中带来时序的不确定性,并须具备较强的抗噪能力。
隔离器技术传输速率比较
隔离不得给整体系统性能带来任何显著的时序不确定性或时序误差。标准光耦合器的传播延迟为微秒级,可能因器件而异,因温度和寿命而异。光耦合器技术在时序性能方面存在一些根本的不足,而现代数字隔离器采用完全不同的运算原则,其速率也更高。
可以在有所折衷的情况下增加光耦合器的速率。光耦合器的工作原理是,将来自LED的光发送至一种光学透明的隔离材料,并用另一端的光电二极管检测光。光耦合器的速度与光电二极管检波器的速率以及为其二极管电容充电的时间直接相关。减少传播延迟的一种方法是增加发射的光量。通过提高LED电流,可以使延迟减少2或3倍,但其代价是设备功耗会增加,每个数据通道最高将达50 mW。
提高速度的另一种办法是通过使用更薄的隔离栅来减少光传输损耗。为了维持相同的隔离能力,需要增加一层材料,但代价是成本也将增高。更快的光耦合器比标准的低成本光耦合器要贵许多倍。
相反,数字隔离器则是采用标准的高速CMOS工艺,并搭载隔离式片内微变压器。其传输速率自然比光耦合器快很多。较高的速度是电路和设计与生俱来的特点,不需要更复杂、成本更高的隔离材料也可实现更高的速度。变压器可以以最高150 Mbps的传输速率传递数据,传播延迟低至32 ns,功耗<5 mW,开关速率为25 kHz或以上。速度更快的另一个好处是,通道间的匹配优于5 ns,比标准光耦合器高出了一个数量级,仅以大约一半的单位通道成本即可实现比光耦合器快3至4倍的卓越性能。
隔离的抗噪性
在电机驱动系统中,隔离还提供了一个分离噪声源的机会,方法是以电流方式将噪声从功率开关电路和控制电路之中隔离开来。以下各项之间有安全隔离需求:高压总线、线路电压和用户界面,以同时保护人、保护其他设备。还需要在功能上使高端开关和低端开关与控制电路相隔离。隔离元件必须能提供必要的隔离,同时也需对嘈杂环境不敏感。
衡量隔离器分离地域之间高速噪声的能力的指标一般称为共模瞬变抗扰度(CMTI)。CMTI旨在衡量一个隔离器在隔离器数据通信不被噪声打断的情况下,对隔离栅中的电压噪声的抑制能力。其单位是kV/μs瞬变。
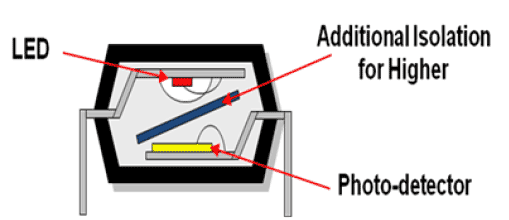
图2. 光耦合器内部结构。
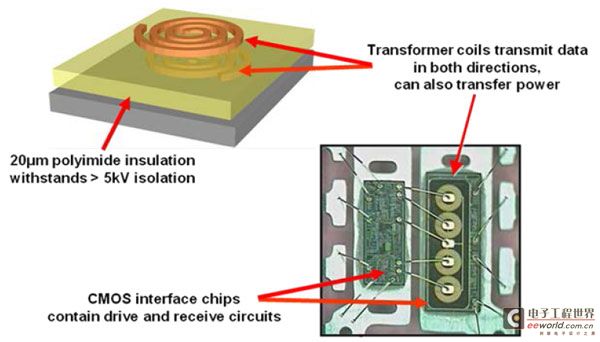
图3. 基于变压器的数字隔离器的结构。
电压瞬变噪声跨越隔离栅的路径一般是寄生电容跨过隔离器中的隔离栅。光耦合器的CMTI一般较差,为15 kV/μs。一些现代数字隔离器采用电容耦合数据隔离技术,其信号和共模噪声使用同一路径。基于变压器的隔离器(如ADI的iCoupler数字隔离器)的信号路径不同于噪声路径,其CMTI的值一般为50 kV/μs或以上。
隔离材料和可靠性
数字隔离器采用晶圆CMOS工艺制造,仅限于常用的晶圆材料。非标准材料会使生产复杂化,导致可制造性变差且成本提高。常用的绝缘材料包括聚合物(如聚酰亚胺PI,它可以旋涂成薄膜)和二氧化硅(SiO2)。二者均具有众所周知的绝缘特性,并且已经在标准半导体工艺中使用多年。聚合物是许多光耦合器的基础,作为高压绝缘体具有悠久的历史。
安全标准通常规定1分钟耐压额定值(典型值2.5 kV rms至5 kV rms)和工作电压(典型值125 V rms至400 V rms)。某些标准也会规定更短的持续时间、电压浪涌(如10 kV峰值并持续50 μs)作为增强绝缘认证的一部分要求。聚合物/聚酰亚胺隔离器可提供最好的隔离特性(见表1)。
表1. 隔离材料性能比较
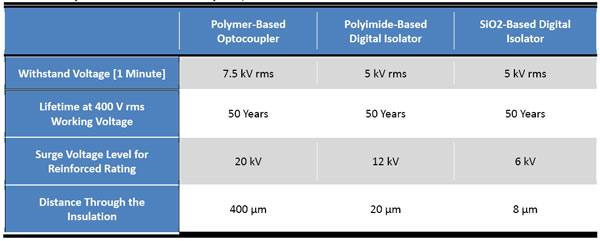
聚酰亚胺数字隔离器与光耦合器类似,在典型工作电压下,工作寿命超过电机,额定使用寿命为50年。SiO2隔离器的工作寿命与之接近,但是,对高能浪涌的保护能力却较弱。
在高温连续使用的情况下,影响光耦合器寿命的可能不是隔离材料的分解而是LED磨损。当温度>85℃时,工作1万小时,光耦合器的电流传输比(CTR)将下降10%至20%。10万小时时,CTR可能会下降一半或以上。
集成可能性
光耦合器LED和优化的光检波器不兼容低成本CMOS技术。要集成带去饱和检测功能的栅极驱动、用∑-△ADC实现隔离电流检测以及多向数据流等其他功能,就必须采用多芯片解决方案,结果将使带这些功能的光耦合器变得非常昂贵。采用CMOS技术和隔离式变压器的数字隔离器可以随着集成度的提高而自然而然地添加这些功能。由于变压器也可用来发射隔离功率,因此,可从相同的封装发射高端功率,而无需会给某些应用带来问题的自举。目前,市场上有基于变压器的数字隔离器,在单个封装中集成了dc/dc转换器、∑-△ ADC、栅极驱动器、I2C、RS-485收发器、RS-232收发器和CAN收发器,使电机控制系统同时实现了尺寸和成本的优化。
实用的应用电路
展示了栅极驱动、通信和反馈信号隔离的典型驱动电路如图4所示。在该系统中,隔离的∑-△ ADC用来测量电机绕组电流,数字位流则由电机控制IC上的数字过滤电路进行处理。位置编码器包含一个ASIC,由其通过一个隔离式RS-485接口将位置和速度数据发送给电机控制IC。其他隔离式串行接口包括连接PFC的I2C接口以及连接前面板的隔离式RS-232链路。在此例中,PWM信号与逆变器模块隔离,IGBT由一个嵌入该模块中的电平转换栅极驱动器驱动。
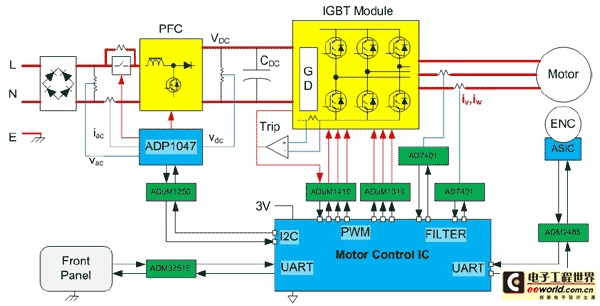
图4. 典型的中型工业电机驱动系统。
数字隔离器工业电机驱 相关文章:
- Windows CE 进程、线程和内存管理(11-09)
- RedHatLinux新手入门教程(5)(11-12)
- uClinux介绍(11-09)
- openwebmailV1.60安装教学(11-12)
- Linux嵌入式系统开发平台选型探讨(11-09)
- Windows CE 进程、线程和内存管理(二)(11-09)