相控阵成像的基本原理
时间:10-02
整理:3721RD
点击:
相控阵成像的基本原理常规超声仪器和相控阵超声仪器都使用高频声波,核查被测样件的内部结构或测量样件的厚度。它们都以物理学中支配声波传播的相同的基本法则为基础。


这两种超声技术都使用相似的概念表示超声数据。无损检测中使用的常规超声仪器通常包含一个既用于生成又用于接收高频声波的单激活晶片,或者包含一对晶片,一个用于发射,另一个用于接收。一套典型的仪器设备包含一个用于生成和接收超声信号的单通道脉冲发生器和接收器,以及一个与在机显示和测量模块配合使用的整合型数字式采集系统。在较高级的设备中,多个脉冲发生器和接收器通道可与一组探头一起使用,以增加覆盖区域,评价不同的深度或缺陷方向,而且可提供更多的报警输出。在更高级的系统中,常规超声技术可与定位编码器、控制器,以及作为成像系统一部分的软件结合在一起使用而相控阵仪器由于要为带有16个晶片到256个晶片的探头提供脉冲激励的方式(聚焦法则),一般来说都具有多通道的性能。与常规探伤仪不同的是,相控阵系统可以使来自一个探头的声波以多种不同的折射角度进行扫查,或沿线性声程进行扫查,还可以使声波在一系列不同的深度位置上动态聚焦,从而增强了检测设置的灵活性和性能。 相控阵仪器这种使用单个探头生成多个声程的超常能力,不仅增强了在探测方面的优势,而且还自然获得了“显示”检测过程的特点,即为检测区域创建图像的能力。 相控阵成像的特性可以使用户观察到相对的点到点的变化以及多角度的缺陷响应,从而有助于缺陷的辨别与定量。这种技术本身从表面上看似乎极具复杂性,但它无需使用常规超声波检测方法经常需要使用的复杂的支架与多个探头,从而在实际上不仅简化了扩大检测覆盖区域的过程,而且还提高了检测的性能。以下各个小节进一步说明了常规超声与相控阵超声数据表达的基本形式。 A扫描数据
所有超声仪器一般都会记录回波的两项基本参数:回波的大小(即波幅)以及在时间轴上相对于零点产生回波的位置(脉冲传送时间)。而脉冲传送时间通常又与反射体的深度或距离相关,并以被测材料的声速为基础。这三者之间的关系表现为以下公式:距离=声速×时间超声波形数据最基本的表现形式是A扫描,或称波形显示。在波形显示图中竖轴代表波幅,横轴代表时间,回波波幅及其渡越时间数据在横轴和竖轴形成的简单的栅格中被绘制成曲线图形。图3中的示例为显示检波波形的A扫描;A扫描中也会使用未经检波的射频波形。屏幕上的红色线段表示门,闸门的作用是选择波形曲线的一部分进行分析,一般是对回波波幅和/或深度进行测量。

图3 A扫描数据
单值B扫描
表现A扫描数据的另一种方式是通过单值B扫描。这种图像形式通常出现在常规探伤仪和腐蚀测厚仪的屏幕上,表现反射体的深度相对于它们的线性位置产生变化的情况。当探头在工件上扫查时,厚度数据会随着时间或探头位置的变化被绘制成图像,从而可提供工件的深度剖面图。将超声数据与探头的实际位置结合起来,可以绘出一个成比例的图形。在这个图形中,可以找到并跟踪被测工件上的具体区域所对应的数据。这种位置跟踪一般是通过被称作编码器的电子机械装置来完成的。有些编码器被置于支架上,需要进行手动扫查。有些编码器被置于自动系统中,探头的移动由可编程电动控制扫查器来完成。在这两种情况下,编码器都会根据用户定义的扫查方式以及步进分辨率,记录下每次进行数据采集的位置。图4中的B扫描显示了对应于试块中横通孔位置的两个较深的反射体和一个较浅的反射体。

图4 B扫描数据
横截面B扫描
横截面B扫描是提供测试样件在单轴方向上的详细信息的端视图。这种图像较前面介绍的单值B扫描提供了更多的信息。绘制这种图像,不能仅使用闸门区域内的单一测量值,而需将每个探头位置的所有A扫描波形都数字化。在对应于渡越时间或探头的实际编码位置上,可以绘出连续的A扫描,从而生成扫查所经过区域的横截面图像。这样用户就可以看到样件内近表面和远表面中反射体的图像。使用这个技术,通常可存储每个位置的完整波形数据,还可以从图像中调用这些数据用于进一步评价或验证。要做到这点,需要将波形中的每一个数字化的点绘制成图,以使代表信号波幅的不同颜色出现在适当的深度位置上。相继出现的A扫描被数字化,不同的数据被分配给不同的颜色,并以用户定义的间隔(渡越时间或位置)被“排列”在一起,形成一个真实的横截面图像(参见图5)。

图5 横截面B扫描
线性扫描
相控阵系统通过沿线性阵列探头的长边所进行的电子扫查,在无需移动探头的情况下,可创建一个横截面剖面图。当以序列方式应用每个聚焦法则时,相关的A扫描被数字化并被绘制成图。相继的孔径被“排列”在一起,生成一幅实时横截面图像。实际上,这种电子扫查是实时进行的,因此在探头进行物理位移的同时,用户会在屏幕中连续看到实时横截面图像。图6为一幅使用64晶片线性相控阵探头进行检测时得到的图像。

图6 垂直声束线性扫查 在这个示例中,用户将聚焦法则以如下方式编程:16个晶片为一个孔径,下一个孔径包含向前错一个晶片的16个晶片,依次类推,序列发射是对这些孔径按顺序连续触发的过程。这样会生成49个单个波形,这些波形排列在一起,可以创建一个在探头1.5英寸(37毫米)长边方向上的实时横截面图像。也可使所有晶片以某个固定角度发出声束进行扫查(参见图7)。


图7 角度声束线性扫查上述这种方法在自动焊缝检测中非常有用。使用带楔块的64晶片线性相控阵探头,可以用户定义的角度(通常为45、60或70度)生成横波。通过在探头长边方向上对孔径进行序列触发,无需在扫查过程中增加探头到焊缝中线之间物理意义上的距离,即可采集到完整的焊缝体积数据。这样就完成了在焊缝长度方向上的单扫检测。
C扫描检测
数据的另一个图像表现形式是C扫描。C扫描是一个两维数据图像,表现为被测样件的顶视图或平面图。C扫描在图像显示方面与X光图像极为相似,被测样件的每一点都被映射到图中相应的位置,每个位置会由不同的颜色表现其在闸门内信号的波幅或深度。通过跟踪数据在XY坐标平面上的置,可以为平面工件生成平面图像;通过跟踪轴位置与角度位置,可以为柱面工件生成平面图像。对于常规超声,使用带有编码器的机械扫查器,可根据适当的步进分辨率(步距),跟踪探头的坐标位置。相控阵系统生成的C扫描与常规探头生成的C扫描极为相似。使用相控阵系统,一般情况是探头沿一个轴做物理意义上的位移,而在另一个轴的方向上,声束会根据聚焦法则序列进行电子扫查。同常规C扫描一样,闸门内有可能存在缺陷的区域的信号波幅或深度数据会被收集起来。进行相控阵检时,在使用编制好的声束孔径进行每个聚焦法则序列触发的过程中,所采集的数据被绘制成图。图8是使用装有零度角楔块的64晶片5MHz线性阵列探头进行检测时为试块生成的C扫描。每个聚焦法则的孔径由16个晶片组成,每次脉冲触发时,孔径会向前移动一个晶片。这样会生成49个数据点,这些数据点会被绘制成沿探头的37毫米(1.5英寸)长度方向上的图像(图8中,水平方向)。当探头以直方式向前移动时,会出现平面C扫描视图。在需要将扫描图像中的几何图形点与实际工件上的位置精确对应时,通常要使用编码器,虽然在很多情况下,通过非编码的手动扫查也可以得到有用的息。虽然由于相控阵的有效声束尺寸较大,其图像的分辨率可能不会完全与常规C扫描图像等同,但是我们要考虑到相控阵技术的其它优点。
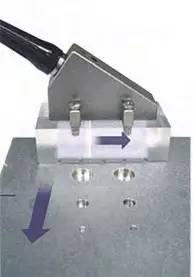

图8 使用64晶片线性相控阵探头得到的C扫描数据图像
相控阵系统为便携式设备,可被方便地携带到检测现场,而常规系统不能做到这点,而且购买相控阵系统的费用只为购买常规系统的三分之一。此外,通常来说只需几秒钟即可生成相控阵图像,而常规水浸扫描图像的生成需要几分钟。 线性相控阵探头还经常用于在焊缝长度方向上进行的折射横波检测。图9显示一个安装在角度楔块上的64晶片2.25MHz相控阵探头,这个探头可以用户定义的角度,一般为45、60或70度,创建波。如果探头垂直于焊缝放置,则其孔径会在探头的长边方向上被序列触发。这样,无需以机械方式在垂直于焊缝中线的方向上移动探头,就可以有效地使折射横波通过整个焊缝体积。通过在平行于焊缝的方向上滑动探头,可使整个焊缝体积的数据显示在屏中。使用编码器,数据可被绘制成如C扫描形式的图像。这类图像中反映反射体的波幅随孔径位置(Y轴)及在焊缝方向上经过的距离(X轴)而变化的情况。这种扫查形式通常被称为“单线扫查”。要生成可重现的结果,建议使用一个机械扫器。在图9中,视图上部表现的是声波在整个焊缝长度方向上遇到未磨平的焊缝底部得到反射而生成的图像。图中的A扫描与光标标出了对应于焊缝区域中侧壁未融合缺陷的一个较大的信号指示。

图 9 使用 64 晶片 2.25 MHz 编码探头以 60 度角对焊缝进行单线扫查检测
S扫描 在到目前为止所有已经介绍的图像模式中,只有S扫描是相控阵设备特有的图像。在线性扫描中,所有聚焦法则以一个固定角度对各个孔径序列进行脉冲触发。而S扫描则是使用固定孔径,在序列变换的不同角度下,以电子方式偏转声束。这种扫描一般使用两种主要式。最熟为人知的,在医学成像中最常见的形式是使用零度界面楔块,以电子方式在不同角度上偏转纵波,生成一个扇形图像,以显示分层缺陷和稍微偏斜的缺陷(参见图9)。


图9 –30°到+30°范围内的S扫描 第二种形式使用塑料楔块增加入射声束的角度,以生成横波。最常见的折射角度范围在30到70度之间。这种技术与常规角度声束检测相似,不同的是声束以一系列不同的角度扫射,而不是以通过楔块形成的单一固定角度传播。其图像显示与线性扇形扫查图像相同,也是被测工件的检测区域的横截面图(参见图10)。


图10 +35°到 +70°范围内的S扫描
生成图像的实际过程也是基于A扫描排列原理,这个原理在前面章节中线性扫描部分中做过介绍。用户定义起始角度、终止角度,以及角度步进分辨率,以生成S扫描图像。要注意孔径需保持不变,每个定义的角度生成一个相应的声束,声束的特性由孔径、频率、阻尼等因素定义。每个角度(聚焦法则)的波形响应被数字化,以颜色编码,并在屏幕上以适当的对应角度绘制,生成一个横截面图像。 实际上,S扫描是实时生成的,因此S扫描是一个会随着探头的移动,持续发生动态变化的图像。这个特点在显示缺陷以及提高缺陷探出率方面非常有用,特别是在探测方向杂乱的缺陷时,因为在检测过程中会同时使用很多检测角度。 融合图像形式 相控阵图像在实时显示体积数据方面的能力极为强大。在电子扫查中,成像过程成为真正的数据实时显示过程,而且可被用于手动和自动两种系统中,以提高缺陷的检出率。特别需要指出的是,功能更为强大的自动相控阵仪器不仅具有显示多个图像类型的功能,还可存储整个检测过程中得到的完整原始波形信息,从而可以在扫查完成后,对检测结果进行分析。因为所有超声波形数据都被收集、存储起来,因此在任何检测地点进行的扫查后分析,都可以使用相应的A扫描信息重建S扫描、C扫和/或B扫描。例如,图11的屏幕同时显示了焊缝形状的检波A扫描波形、S扫描以及平面C扫描图像。

图11 多图像类型的显示 扫查速度和数据采集 在生成B扫描或C扫描时,可以用手移动相控阵探头,也可以通过自动扫查固定装置移动相控阵探头。在这两种情况下,数据采集都可以仅基于仪器的刷新率自由进行,也可以通过使用电子机械编码器,基于探头的位置进行。如前面所述,使用基于探头实际位置所采集的超声数据可以绘制出成比例的视图,而且还可在被测工件中找到超声数据所对应的具体位置。编码器会记录下相对于用户定义的扫查方式与步进分辨率的每次数据采集的位置。为了避免数据采集过程中出现空白,必须要考虑探头移动的速度以及编码器的距离分辨率(步距)。简言之,仪器的数据采集速率必须高于扫查速度除以编码器分辨率的商。采集速率由仪器的设计和设置决定,其中最重要的两个因素是脉冲重复频率(PRF)和每次采集生成的聚焦法则数量,这两个因素都属于设置变量。脉冲重复频率除以聚焦法则数量得出相控阵系统所允许的最快采集速率。然而所得到的数值还可以根据其它因素如:平均、数字式采样率及处理时间,进一步得到调整。要了解详细情况,请咨询仪器制造商。采集速率被确定后,就可以基于所需的编码器分辨率,计算出最大扫查速度,反之亦然。在扫查速度相对于特定的编码器分辨率过高的情况下出现的扫查效果如图12中的扫描图像所示。 重要事项1.采集速率>扫查速度÷扫查轴分辨率2.如果为所有A扫描都设置了相同的脉冲重复频率,则:采集速率<重复频率÷聚焦法则数量采集速率>扫查速度÷编码器分辨率

图12 扫查速度影响采集速率的示例


这两种超声技术都使用相似的概念表示超声数据。无损检测中使用的常规超声仪器通常包含一个既用于生成又用于接收高频声波的单激活晶片,或者包含一对晶片,一个用于发射,另一个用于接收。一套典型的仪器设备包含一个用于生成和接收超声信号的单通道脉冲发生器和接收器,以及一个与在机显示和测量模块配合使用的整合型数字式采集系统。在较高级的设备中,多个脉冲发生器和接收器通道可与一组探头一起使用,以增加覆盖区域,评价不同的深度或缺陷方向,而且可提供更多的报警输出。在更高级的系统中,常规超声技术可与定位编码器、控制器,以及作为成像系统一部分的软件结合在一起使用而相控阵仪器由于要为带有16个晶片到256个晶片的探头提供脉冲激励的方式(聚焦法则),一般来说都具有多通道的性能。与常规探伤仪不同的是,相控阵系统可以使来自一个探头的声波以多种不同的折射角度进行扫查,或沿线性声程进行扫查,还可以使声波在一系列不同的深度位置上动态聚焦,从而增强了检测设置的灵活性和性能。 相控阵仪器这种使用单个探头生成多个声程的超常能力,不仅增强了在探测方面的优势,而且还自然获得了“显示”检测过程的特点,即为检测区域创建图像的能力。 相控阵成像的特性可以使用户观察到相对的点到点的变化以及多角度的缺陷响应,从而有助于缺陷的辨别与定量。这种技术本身从表面上看似乎极具复杂性,但它无需使用常规超声波检测方法经常需要使用的复杂的支架与多个探头,从而在实际上不仅简化了扩大检测覆盖区域的过程,而且还提高了检测的性能。以下各个小节进一步说明了常规超声与相控阵超声数据表达的基本形式。 A扫描数据
所有超声仪器一般都会记录回波的两项基本参数:回波的大小(即波幅)以及在时间轴上相对于零点产生回波的位置(脉冲传送时间)。而脉冲传送时间通常又与反射体的深度或距离相关,并以被测材料的声速为基础。这三者之间的关系表现为以下公式:距离=声速×时间超声波形数据最基本的表现形式是A扫描,或称波形显示。在波形显示图中竖轴代表波幅,横轴代表时间,回波波幅及其渡越时间数据在横轴和竖轴形成的简单的栅格中被绘制成曲线图形。图3中的示例为显示检波波形的A扫描;A扫描中也会使用未经检波的射频波形。屏幕上的红色线段表示门,闸门的作用是选择波形曲线的一部分进行分析,一般是对回波波幅和/或深度进行测量。

图3 A扫描数据
单值B扫描
表现A扫描数据的另一种方式是通过单值B扫描。这种图像形式通常出现在常规探伤仪和腐蚀测厚仪的屏幕上,表现反射体的深度相对于它们的线性位置产生变化的情况。当探头在工件上扫查时,厚度数据会随着时间或探头位置的变化被绘制成图像,从而可提供工件的深度剖面图。将超声数据与探头的实际位置结合起来,可以绘出一个成比例的图形。在这个图形中,可以找到并跟踪被测工件上的具体区域所对应的数据。这种位置跟踪一般是通过被称作编码器的电子机械装置来完成的。有些编码器被置于支架上,需要进行手动扫查。有些编码器被置于自动系统中,探头的移动由可编程电动控制扫查器来完成。在这两种情况下,编码器都会根据用户定义的扫查方式以及步进分辨率,记录下每次进行数据采集的位置。图4中的B扫描显示了对应于试块中横通孔位置的两个较深的反射体和一个较浅的反射体。

图4 B扫描数据
横截面B扫描
横截面B扫描是提供测试样件在单轴方向上的详细信息的端视图。这种图像较前面介绍的单值B扫描提供了更多的信息。绘制这种图像,不能仅使用闸门区域内的单一测量值,而需将每个探头位置的所有A扫描波形都数字化。在对应于渡越时间或探头的实际编码位置上,可以绘出连续的A扫描,从而生成扫查所经过区域的横截面图像。这样用户就可以看到样件内近表面和远表面中反射体的图像。使用这个技术,通常可存储每个位置的完整波形数据,还可以从图像中调用这些数据用于进一步评价或验证。要做到这点,需要将波形中的每一个数字化的点绘制成图,以使代表信号波幅的不同颜色出现在适当的深度位置上。相继出现的A扫描被数字化,不同的数据被分配给不同的颜色,并以用户定义的间隔(渡越时间或位置)被“排列”在一起,形成一个真实的横截面图像(参见图5)。

图5 横截面B扫描
线性扫描
相控阵系统通过沿线性阵列探头的长边所进行的电子扫查,在无需移动探头的情况下,可创建一个横截面剖面图。当以序列方式应用每个聚焦法则时,相关的A扫描被数字化并被绘制成图。相继的孔径被“排列”在一起,生成一幅实时横截面图像。实际上,这种电子扫查是实时进行的,因此在探头进行物理位移的同时,用户会在屏幕中连续看到实时横截面图像。图6为一幅使用64晶片线性相控阵探头进行检测时得到的图像。


图6 垂直声束线性扫查 在这个示例中,用户将聚焦法则以如下方式编程:16个晶片为一个孔径,下一个孔径包含向前错一个晶片的16个晶片,依次类推,序列发射是对这些孔径按顺序连续触发的过程。这样会生成49个单个波形,这些波形排列在一起,可以创建一个在探头1.5英寸(37毫米)长边方向上的实时横截面图像。也可使所有晶片以某个固定角度发出声束进行扫查(参见图7)。


图7 角度声束线性扫查上述这种方法在自动焊缝检测中非常有用。使用带楔块的64晶片线性相控阵探头,可以用户定义的角度(通常为45、60或70度)生成横波。通过在探头长边方向上对孔径进行序列触发,无需在扫查过程中增加探头到焊缝中线之间物理意义上的距离,即可采集到完整的焊缝体积数据。这样就完成了在焊缝长度方向上的单扫检测。
C扫描检测
数据的另一个图像表现形式是C扫描。C扫描是一个两维数据图像,表现为被测样件的顶视图或平面图。C扫描在图像显示方面与X光图像极为相似,被测样件的每一点都被映射到图中相应的位置,每个位置会由不同的颜色表现其在闸门内信号的波幅或深度。通过跟踪数据在XY坐标平面上的置,可以为平面工件生成平面图像;通过跟踪轴位置与角度位置,可以为柱面工件生成平面图像。对于常规超声,使用带有编码器的机械扫查器,可根据适当的步进分辨率(步距),跟踪探头的坐标位置。相控阵系统生成的C扫描与常规探头生成的C扫描极为相似。使用相控阵系统,一般情况是探头沿一个轴做物理意义上的位移,而在另一个轴的方向上,声束会根据聚焦法则序列进行电子扫查。同常规C扫描一样,闸门内有可能存在缺陷的区域的信号波幅或深度数据会被收集起来。进行相控阵检时,在使用编制好的声束孔径进行每个聚焦法则序列触发的过程中,所采集的数据被绘制成图。图8是使用装有零度角楔块的64晶片5MHz线性阵列探头进行检测时为试块生成的C扫描。每个聚焦法则的孔径由16个晶片组成,每次脉冲触发时,孔径会向前移动一个晶片。这样会生成49个数据点,这些数据点会被绘制成沿探头的37毫米(1.5英寸)长度方向上的图像(图8中,水平方向)。当探头以直方式向前移动时,会出现平面C扫描视图。在需要将扫描图像中的几何图形点与实际工件上的位置精确对应时,通常要使用编码器,虽然在很多情况下,通过非编码的手动扫查也可以得到有用的息。虽然由于相控阵的有效声束尺寸较大,其图像的分辨率可能不会完全与常规C扫描图像等同,但是我们要考虑到相控阵技术的其它优点。
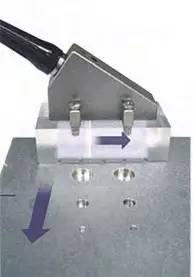

图8 使用64晶片线性相控阵探头得到的C扫描数据图像
相控阵系统为便携式设备,可被方便地携带到检测现场,而常规系统不能做到这点,而且购买相控阵系统的费用只为购买常规系统的三分之一。此外,通常来说只需几秒钟即可生成相控阵图像,而常规水浸扫描图像的生成需要几分钟。 线性相控阵探头还经常用于在焊缝长度方向上进行的折射横波检测。图9显示一个安装在角度楔块上的64晶片2.25MHz相控阵探头,这个探头可以用户定义的角度,一般为45、60或70度,创建波。如果探头垂直于焊缝放置,则其孔径会在探头的长边方向上被序列触发。这样,无需以机械方式在垂直于焊缝中线的方向上移动探头,就可以有效地使折射横波通过整个焊缝体积。通过在平行于焊缝的方向上滑动探头,可使整个焊缝体积的数据显示在屏中。使用编码器,数据可被绘制成如C扫描形式的图像。这类图像中反映反射体的波幅随孔径位置(Y轴)及在焊缝方向上经过的距离(X轴)而变化的情况。这种扫查形式通常被称为“单线扫查”。要生成可重现的结果,建议使用一个机械扫器。在图9中,视图上部表现的是声波在整个焊缝长度方向上遇到未磨平的焊缝底部得到反射而生成的图像。图中的A扫描与光标标出了对应于焊缝区域中侧壁未融合缺陷的一个较大的信号指示。

图 9 使用 64 晶片 2.25 MHz 编码探头以 60 度角对焊缝进行单线扫查检测
S扫描 在到目前为止所有已经介绍的图像模式中,只有S扫描是相控阵设备特有的图像。在线性扫描中,所有聚焦法则以一个固定角度对各个孔径序列进行脉冲触发。而S扫描则是使用固定孔径,在序列变换的不同角度下,以电子方式偏转声束。这种扫描一般使用两种主要式。最熟为人知的,在医学成像中最常见的形式是使用零度界面楔块,以电子方式在不同角度上偏转纵波,生成一个扇形图像,以显示分层缺陷和稍微偏斜的缺陷(参见图9)。


图9 –30°到+30°范围内的S扫描 第二种形式使用塑料楔块增加入射声束的角度,以生成横波。最常见的折射角度范围在30到70度之间。这种技术与常规角度声束检测相似,不同的是声束以一系列不同的角度扫射,而不是以通过楔块形成的单一固定角度传播。其图像显示与线性扇形扫查图像相同,也是被测工件的检测区域的横截面图(参见图10)。


图10 +35°到 +70°范围内的S扫描
生成图像的实际过程也是基于A扫描排列原理,这个原理在前面章节中线性扫描部分中做过介绍。用户定义起始角度、终止角度,以及角度步进分辨率,以生成S扫描图像。要注意孔径需保持不变,每个定义的角度生成一个相应的声束,声束的特性由孔径、频率、阻尼等因素定义。每个角度(聚焦法则)的波形响应被数字化,以颜色编码,并在屏幕上以适当的对应角度绘制,生成一个横截面图像。 实际上,S扫描是实时生成的,因此S扫描是一个会随着探头的移动,持续发生动态变化的图像。这个特点在显示缺陷以及提高缺陷探出率方面非常有用,特别是在探测方向杂乱的缺陷时,因为在检测过程中会同时使用很多检测角度。 融合图像形式 相控阵图像在实时显示体积数据方面的能力极为强大。在电子扫查中,成像过程成为真正的数据实时显示过程,而且可被用于手动和自动两种系统中,以提高缺陷的检出率。特别需要指出的是,功能更为强大的自动相控阵仪器不仅具有显示多个图像类型的功能,还可存储整个检测过程中得到的完整原始波形信息,从而可以在扫查完成后,对检测结果进行分析。因为所有超声波形数据都被收集、存储起来,因此在任何检测地点进行的扫查后分析,都可以使用相应的A扫描信息重建S扫描、C扫和/或B扫描。例如,图11的屏幕同时显示了焊缝形状的检波A扫描波形、S扫描以及平面C扫描图像。

图11 多图像类型的显示 扫查速度和数据采集 在生成B扫描或C扫描时,可以用手移动相控阵探头,也可以通过自动扫查固定装置移动相控阵探头。在这两种情况下,数据采集都可以仅基于仪器的刷新率自由进行,也可以通过使用电子机械编码器,基于探头的位置进行。如前面所述,使用基于探头实际位置所采集的超声数据可以绘制出成比例的视图,而且还可在被测工件中找到超声数据所对应的具体位置。编码器会记录下相对于用户定义的扫查方式与步进分辨率的每次数据采集的位置。为了避免数据采集过程中出现空白,必须要考虑探头移动的速度以及编码器的距离分辨率(步距)。简言之,仪器的数据采集速率必须高于扫查速度除以编码器分辨率的商。采集速率由仪器的设计和设置决定,其中最重要的两个因素是脉冲重复频率(PRF)和每次采集生成的聚焦法则数量,这两个因素都属于设置变量。脉冲重复频率除以聚焦法则数量得出相控阵系统所允许的最快采集速率。然而所得到的数值还可以根据其它因素如:平均、数字式采样率及处理时间,进一步得到调整。要了解详细情况,请咨询仪器制造商。采集速率被确定后,就可以基于所需的编码器分辨率,计算出最大扫查速度,反之亦然。在扫查速度相对于特定的编码器分辨率过高的情况下出现的扫查效果如图12中的扫描图像所示。 重要事项1.采集速率>扫查速度÷扫查轴分辨率2.如果为所有A扫描都设置了相同的脉冲重复频率,则:采集速率<重复频率÷聚焦法则数量采集速率>扫查速度÷编码器分辨率

图12 扫查速度影响采集速率的示例